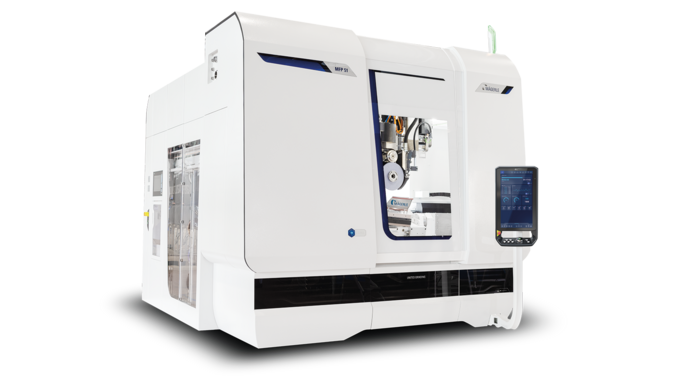
Portal tool magazine
In its basic version this sturdy grinding center comes with an integrated tool changer in a gantry design with 68 positions. The magazine can be flexibly loaded with various grinding wheels, diamond rolls, measuring probes and tools for drilling and milling operations. The large capacity of the tool changer enables efficient machining of several different workpieces without altering the tooling.
Tool identification
An identification system for grinding wheels and tools is optionally available. The tool is inserted into a holder in the loading station. The data stored on an RFID chip is securely imported prior to the loading process. The chip is written with the current data when the grinding wheel is unloaded. The tool identification eliminates the probability of errors when entering the tool data in the machine, guaranteeing safe and uninterrupted operation.
Simultaneous tool & dresser roll changer
Very short process times are achieved with the high-speed spindle, which allows speeds of up to 12,000 rpm, and the overhead dresser integrated into the grinding support. The grinding wheels and diamond dressing rolls are simultaneously or individually exchanged with a double gripper for the individual machining steps. The compact tool holding fixtures allow an efficient grinding process and the continuously dressed grinding wheel enables high removal rates with high profile accuracy over long cuts. Additional time savings are achieved with the overhead dresser, thanks to elimination of the dressing process after the grinding cycle and the movement times to the dresser.
Process-optimized coolant supply
The 2-axis controlled coolant nozzle enables an optimal coolant supply to the tool or workpiece. Nozzles are available on the grinding support for drilling and milling tools, and a coolant supply can be provided through the spindle. The coolant supply can be ideally adapted to the process with the optionally available nozzle changer, enabling optimal grinding results.
- Suitable for multiple-side and complete machining
- Interfaces for automated cell production with robot connection
- 68-position tool changer
- Automatic overhead dressing
- Grinding, milling, drilling and measuring in a single clamping
- Compact 5/6-axis grinding center
- Optional nozzle changer
C.O.R.E. – Customer Oriented REvolution
Your Benefits
- Intuitive, user-friendly, and efficient operation
- Access to important information directly at the control panel (e.g. production progress, task details, etc.)
- Reduced programming when exchanging data between C.O.R.E. machines
- Use of UNITED GRINDING Digital Solutions™ products directly on the machine
- Fast support thanks to direct interaction with our Customer Care team on the machine