La technologie actuelle: attractive à tous égards
Chez la société Apex Tool Group GmbH (ATG) à Westhausen, la rectifieuse cylindrique S31 Studer s’avère véritablement universelle. De la pièce unique à la moyenne série, elle rectifie de façon économique et flexible les arbres de transmission et de commande équipant des outils de montage électriques et pneumatiques Cleco. Cleco fait partie des six marques mondiales d’outils motorisés et manuels ATG
A Westhausen, dans la salle d’expo d’Apex Tool Group – anciennement Cooper Power Tools –, la gamme complète des différents outils de montage Cleco est impressionnante. Parmi eux figurent des outils de vissage en version droite, coudée et à poignée-pistolet, à entraînement pneumatique et électrique, alimentés au choix par câble ou batterie. Il existe en outre des stations de montage complètes dont la commande intégrée affiche sur écran des instructions de montage des vis, fournit les paramètres requis pour le vissage, les surveille et les documente. Les outils de vissage sont mis en œuvre par exemple pour monter des moteurs thermiques et électriques, des carrosseries, transmissions et groupes hydrauliques dans la construction automobile et l’aéronautique, mais aussi dans le montage automatisé des roues sur les véhicules. Pour répondre aux exigences actuelles, pointues, de haute sécurité des processus, et de documentation de ces derniers, le fabricant équipe les outils de montage de capteurs servant à mesurer les couples ainsi que d’un système de transmission des données par câble ou par radio (WLAN). Comme en fait état Niko Schindelarz, Supervisor Machining, les outils de montage Cleco jouissent chez de nombreux constructeurs industriels d’une réputation de très haute qualité, robustesse, longévité et fiabilité. Un autre atout important, poursuit Niko Schindelarz, est certainement la grande profondeur de fabrication chez Apex. La quasi-totalité des composants importants pour le fonctionnement des outils de vissage est produite dans l’entreprise à Westhausen. Cela concerne surtout les arbres moteurs et de transmission, les leviers, soupapes, cames et carters.
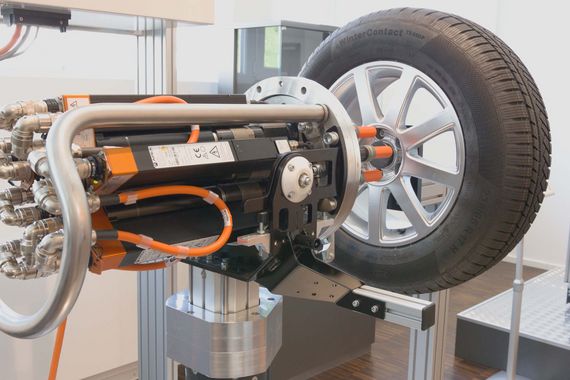
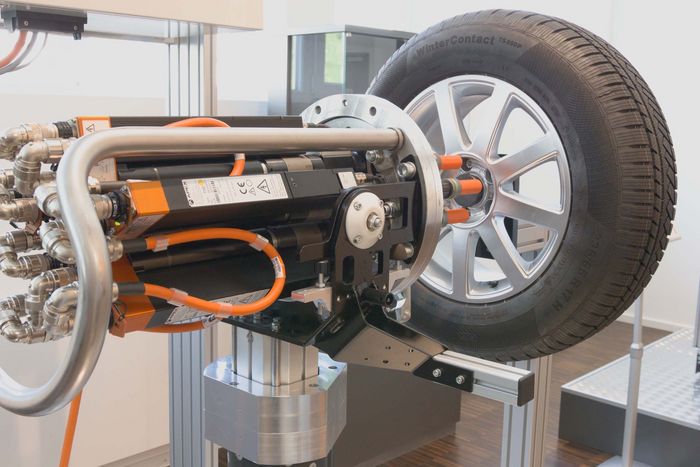
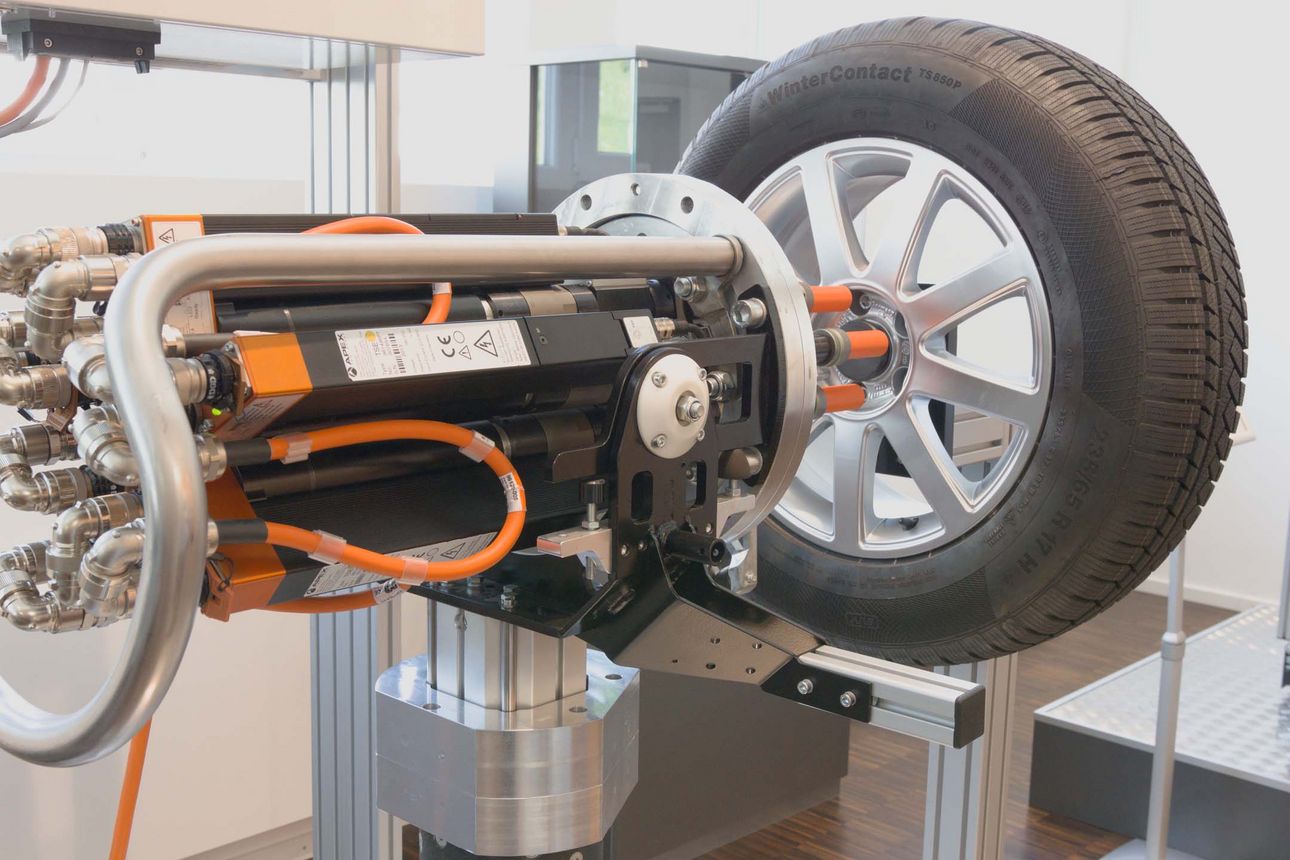
Flexibilité pour les variantes et les équipements individuels
«Vu le grand nombre de variantes et la demande croissante d’équipements individuels, nous sommes mis au défi de produire des composants en petites séries, voire en pièces uniques, et ceci dans de très courts délais», relate Johannes Mäule, Production Engineer à Westhausen. Et de poursuivre en indiquant que cela concerne toutes les étapes et procédés de fabrication, du tournage à la rectification en passant par l’alésage et le fraisage. «Nos arbres pour moteurs et transmissions notamment, nous devons les rectifier à quelques microns près. C’est uniquement à cette condition que nous pouvons faire du fonctionnement extrêmement silencieux de nos outils de vissage et de leur grande longévité une réalité», ajoute Niko Schindelarz. Or il y a encore quelques mois de cela, l’opération était très complexe. Pour la rectification cylindrique, seule une rectifieuse confirmée était disponible, dont l’acquisition remontait au début des années 1980. Pour rectifier le grand nombre d’arbres longs de 30 à 650 mm et d’un diamètre compris entre 3 et 65 mm, il fallait – opération laborieuse – régulièrement recaler la machine à la main. Cette situation faisait obstacle à une fabrication flexible et adaptée aux besoins. «Et surtout la rentabilité en souffrait de plus en plus. Les temps de calage étaient généralement deux à trois fois plus longs que les temps d’usinage», explique Johannes Mäule. En outre, Niko Schindelarz signale que les précisions des diamètres et de la cylindricité ne pouvaient être atteintes, surtout avec les arbres longs et minces, qu’au prix d’efforts non négligeables. Il indique ensuite que seuls y parvenaient des spécialistes expérimentés, maîtrisant la rectification depuis de nombreuses années. «Or ces spécialistes passent actuellement le relais et vont partir à la retraite ces prochaines années. Avec pour effet que nous ne disposerons plus de leur savoir-faire. Entre-temps, la formation de la relève se concentre toutefois sur des aspects autres qu’il y a encore quelques années. Les interventions manuelles sur les machines sont plutôt indésirables, la priorité va à la programmation et au paramétrage optimal des processus», indique Niko Schindelarz.
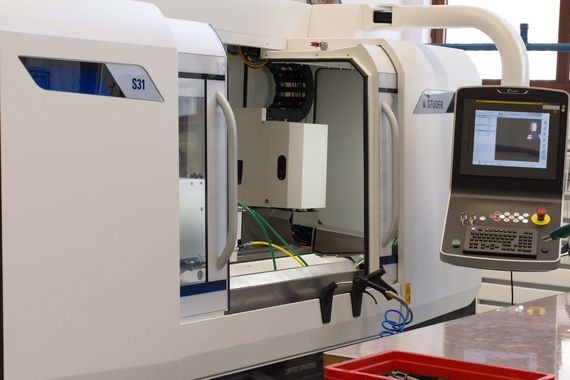
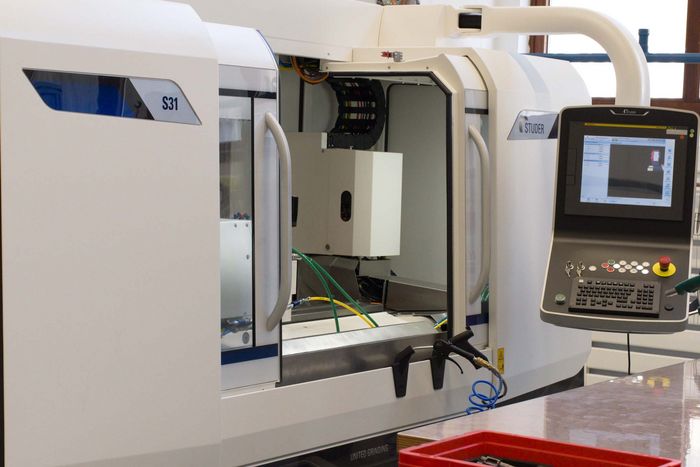
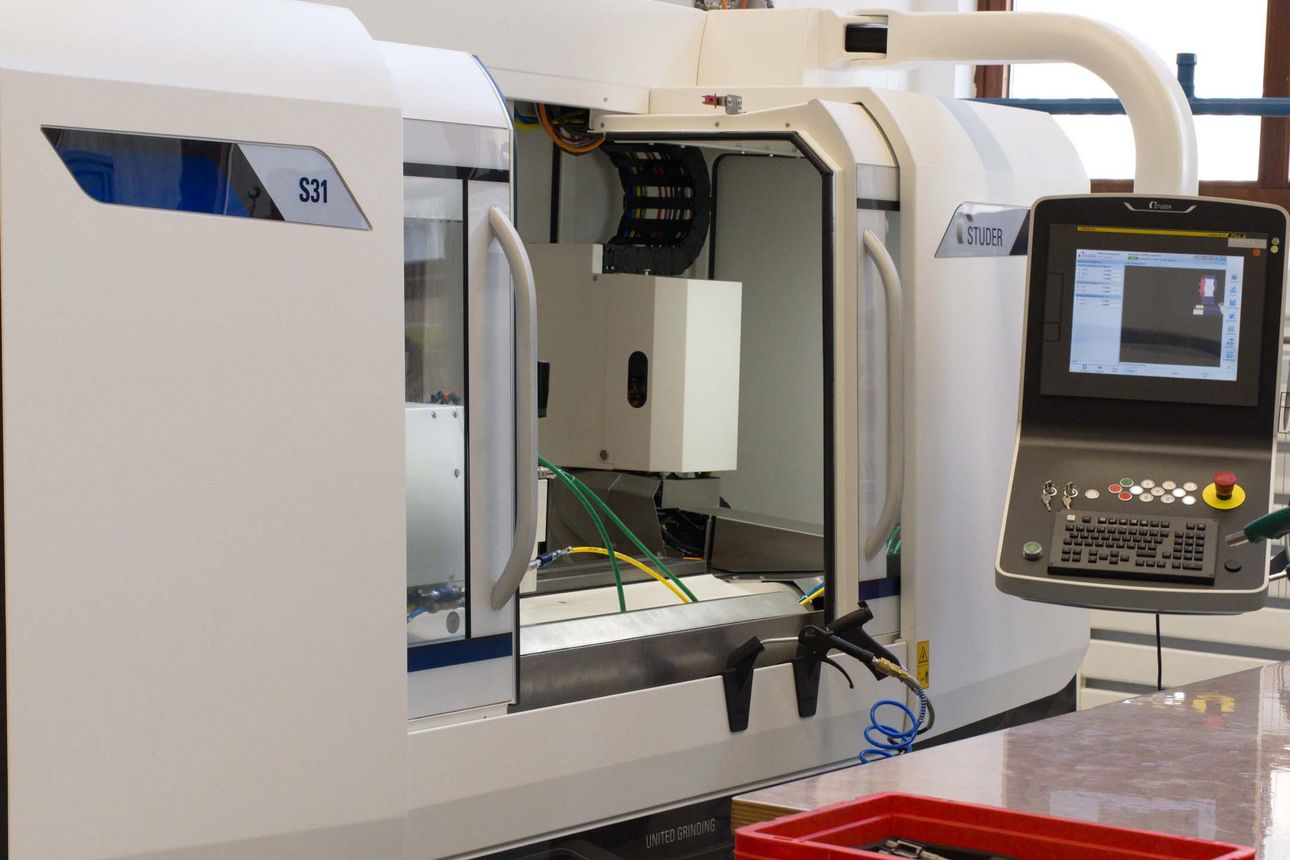
Changement de génération
Face à cette situation, les responsables chez Apex ont décidé d’investir, concernant la rectification ainsi que d’autres procédés d’usinage, dans une technologie actuelle. Car de cet environnement technique métamorphosé naissent de multiples exigences supplémentaires envers les machines et les installations de fabrication. Outre une grande flexibilité, cela concerne par exemple les possibilités de surveiller des processus de façon automatisée, ainsi que de transmettre des données processuelles et de production dans un réseau numérique – entendez l’usine intelligente –. «En outre, ce n’est qu’avec des technologies actuelles et axées sur le futur que nous pouvons être un employeur intéressant et enthousiasmer la relève, dont il y a urgemment besoin, à entrer en activité dans notre entreprise», complète Niko Schindelarz. Après avoir comparé en profondeur différents concepts de machine, lui et Johannes Mäule ont décidé d’investir dans une rectifieuse cylindrique universelle S31 Studer.
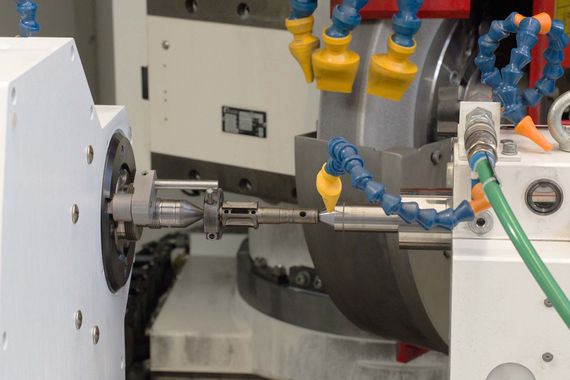

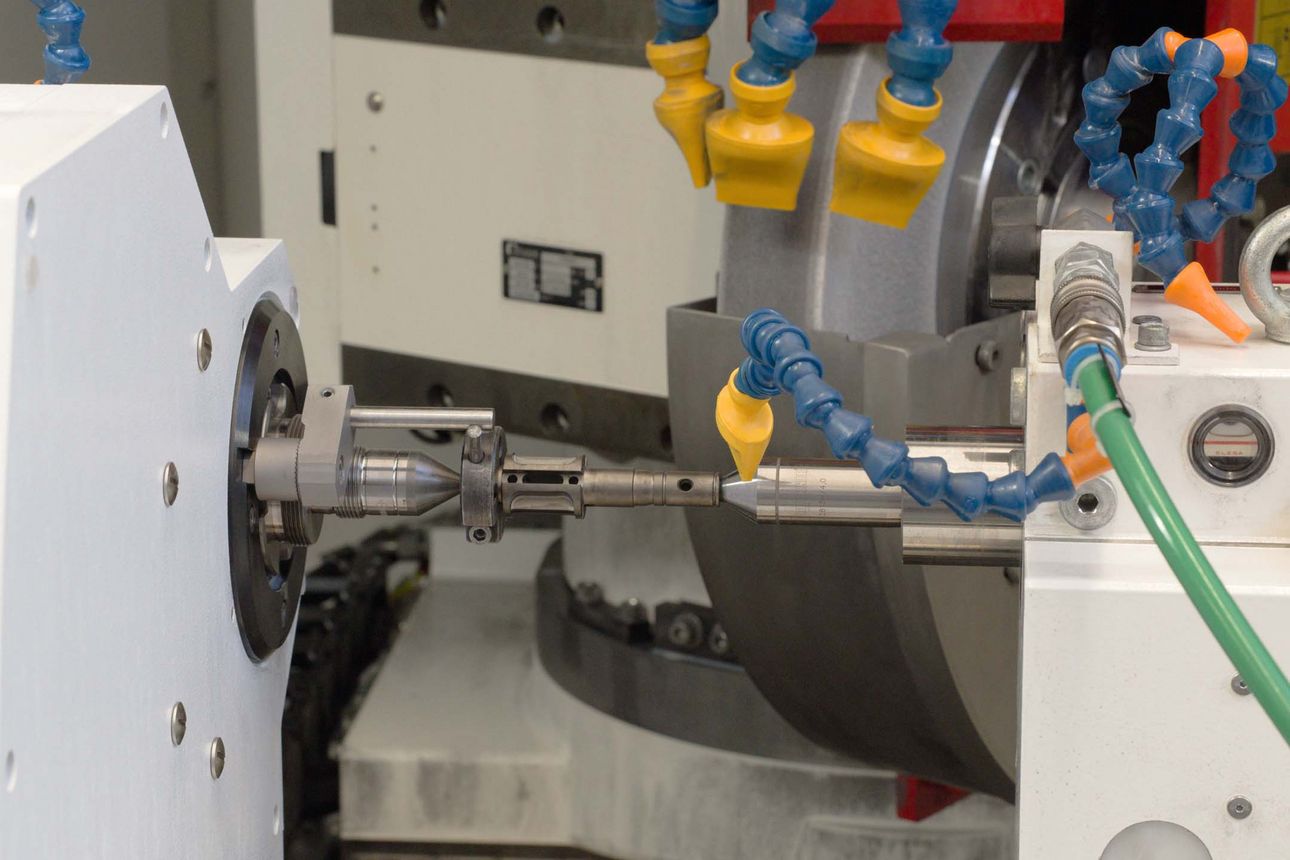
Haute flexibilité grâce à des temps de calage courts
Comme le relate Niko Schindelarz, il s’agissait dans un premier temps de réaliser une analyse soignée des besoins pour obtenir, des responsables commerciaux au sein du groupe américain, le feu vert budgétaire nécessaire. «Il nous a été facile de prouver clairement, avantages d’exploitation à l’appui, que cet investissement initial – plus lourd comparé à des produits concurrents –, allait rapidement s’avérer rentable», déclarent de concert Johannes Mäule et Niko Schindelarz. A Westhausen, les techniciens de fabrication peuvent dans l’intervalle produire l’ensemble de la gamme d’arbres sur une seule machine. Malgré son capotage intégral, la rectifieuse cylindrique S31 est très aisément accessible pour charger les pièces et monter les meules de rectification. Niko Schindelarz et avec lui les opérateurs de la machine font l’éloge surtout de l’excellente ergonomie de travail. Les techniciens de fabrication à Westhausen profitent ainsi de temps de changements de séries nettement plus courts comparés aux anciennes rectifieuses. La fonction spéciale Quick-Set, disponible uniquement sur les rectifieuses Studer, y contribue aussi de façon essentielle. Cornelius Wecht, responsable des Ventes Sud Allemagne chez Studer, s’en fait l’écho: «Grâce au Quick-Set, la commande enregistre les dimensions précises de toutes les meules mises en œuvre sur la rectifieuse. Cela permet de caler rapidement les meules déjà utilisées plusieurs fois et dressées à maintes reprises, et de les réutiliser sans délai. Après un changement de meule, la commande en connaît les dimensions exactes, un nouveau mesurage ou même un dressage de meule sur la machine disparaît.» La possibilité de dresser les meules profilées directement sur la rectifieuse cylindrique est considérée par les rectifieurs de Westhausen comme un autre avantage de la machine. Le logiciel StuderDress prévoit des cycles de dressage à cette fin. Sur les meules profilées, ces cycles permettent de dresser par rotation uniquement les géométries respectivement requises. Comme Niko Schindelarz le confirme, d’une part cela raccourcit les temps de rééquipement et temps secondaires. D’autre part cela accroît les précisions et améliore les surfaces des composants rectifiés.
Idéal pour la programmation à l’atelier
Pour Niko Schindelarz, c’est surtout aussi le concept de commande de la rectifieuse cylindrique S31 qui offre d’éminents avantages. Comme il le souligne, l’interface opérateur est très aisée à comprendre. Les opérateurs et programmeurs sont guidés de manière claire, dans les différents champs de saisie, au moyen de graphiques et de boîtes de dialogue. La commande dispose en outre d’une base de données contenant tous les paramètres nécessaires pour rectifier. «Nous appelons cela StuderTechnology Integrated», explique Cornelius Wecht à ce sujet. A l’aide des géométries de pièces ainsi que des précisions et de la qualité superficielle exigées, l’opérateur machine choisit les paramètres proposés par le logiciel. A l’aide de ces paramètres, la rectifieuse cylindrique livre toujours, et avec fiabilité, un résultat de rectification exploitable. Le rectificateur expérimenté peut à tout moment modifier les paramètres spécifiés et continuer ainsi à optimiser le processus de rectification. «De la sorte, la S31 s’avère idéale pour la pratique en atelier. Chez nous, chaque spécialiste formé à l’usinage par enlèvement de copeau peut aussi travailler sur la rectifieuse cylindrique. Des connaissances spéciales sur la rectification ne sont pas nécessaires. Cela nous procure une très haute flexibilité», indique Niko Schindelarz.
Universalité grâce à l’axe B
Sur la rectifieuse cylindrique S31 utilisée chez Apex Tool Group à Westhausen, la poupée porte-meule est équipée d’un axe B. Il est possible de faire pivoter la poupée porte-meule par pas de 1°. Deux entraînements de broche sont installés, chacun équipé d’une meule servant à la plongée droite et à la plongée oblique. Cela aussi contribue à des temps de changements de séries courts et à une très haute flexibilité. «En une séquence, nous pouvons rectifier une pièce en plongée droite et oblique sans réglage intermédiaire. Cela permet d’usiner entièrement et jusqu’à la fin, en un seul serrage, la presque totalité des composants», indique Niko Schindelarz pour expliquer les avantages de l’axe B, et de souligner expressément: « avec l’équipement que nous avons choisi pour couvrir nos besoins, la rectifieuse S31 a entièrement mérité au final son attribut d’’universelle’. S’il existe une rectifieuse cylindrique méritant la caractéristique d’universelle, c’est bien la Studer S31. » En près de cinq mois maintenant, la rectifieuse cylindrique S31 en service à Westhausen a prouvé qu’elle remplit intégralement les exigences poussées émises par les constructeurs d’outillage.
Conseils et services exemplaires
Johannes Mäule évoque un autre aspect important des investissements dans des installations de fabrication : «Pour une technologie spéciale comme la rectification, les techniciens de fabrication ne détiennent la plupart du temps que des connaissances techniques générales. Cela concerne surtout les caractéristiques d’équipement innovantes sur les machines et leur avantages spécifiques par rapport aux exigences individuelles.» Niko Schindelarz ajoute que le travail de recherche sur la technologie de rectification actuelle n’a, dans un premier temps, pas été chose facile. «Mais voilà, les spécialistes de chez Studer nous ont conseillé très en détail et surtout de façon ouverte et sincère. Ensemble, nous sommes parvenus à élaborer en quelques étapes la configuration optimale, pour nous, de la rectifieuse cylindrique», poursuit-il. Cela a instauré la confiance qu’il fallait pour investir sereinement dans cette machine au final complexe qu’est la rectifieuse cylindrique S31. «L’important pour nous était aussi que le service après-vente et les conseillers techniques soient aussi représentés au niveau régional, qu’ils puissent nous conseiller et nous assister en matière de fabrication dans un court délai. Seule cette méthode garantit que cet investissement, actuel et tourné vers l’avenir, dans la S31, s’avère rentable dans la durée», souligne Niko Schindelarz. Il indique pour résumer que Studer, ses spécialistes et sa rectifieuse cylindrique universelle S31 ont satisfait à l’intégralité des critères fixés.