Schleifbrand vermeiden
Zu grosse Wärmeentwicklung im Schleifprozess kann zu thermischen Schäden am Werkstück führen, die oftmals die Verschrottung des betroffenen Bauteils zur Folge hat. Wie es zu dieser Wärmeentwicklung kommt, wie Sie sie feststellen und wie Sie diese vermeiden können, lesen Sie in diesem Motion Blog.
Definition von Schleifbrand
Beginnen wir mit der Definition von Schleifbrand und seinen Entstehungsursachen. Beim Schleifen gehärteten Stahls wird nahezu die gesamte von der Schleifspindel aufgebrachte Energie in Wärme umgesetzt. In idealen Schleifprozessen sollte diese Wärme durch die entstehenden Späne und den Kühlschmierstoff abgeleitet werden. Kann die Wärme jedoch nicht effektiv abgeführt werden, dringt sie in das Werkstück ein und kann dort zu Gefüge- oder Randzonenveränderungen führen, die als Schleifbrand oder thermische Schäden bekannt sind. Diese Veränderungen können Schleifrissen und Zugspannungen Vorschub leisten und führen, sofern erkannt, zwangsläufig zur Verschrottung des betroffenen Bauteils. Dies ist notwendig, um schwerwiegende Folgen, die durch fehlerhafte Bauteile in kritischen Anwendungen wie Motoren, Turbinen und Maschinen entstehen könnten, zu vermeiden.
Entstehung von Schleifbrand
Schleifbrand stellt ein komplexes Phänomen dar, das durch eine Vielzahl von Faktoren beeinflusst wird. Um Schleifbrand zu vermeiden, ist die korrekte Auswahl der Schleifparameter entscheidend, ebenso wie die Verwendung passender Schleifscheiben, eine wirksame Kühlung, das Verständnis für die Materialeigenschaften, die Beherrschung der Schleifmaschine und die fachgerechte Ausführung der Schleiftechnik. Durch sorgfältige Überwachung und gezielte Anpassung dieser Faktoren lässt sich die Qualität des Schleifergebnisses steigern und das Risiko von Schleifschäden reduzieren.
Im Folgenden werden die wesentlichen Ursachen erörtert.
1. Schleifparameter
Bei allen Schleifverfahren zählt die Umfangsgeschwindigkeit vc der Schleifscheibe, angegeben in Metern pro Sekunde, zu den wichtigsten Schleifparametern. Eine grundlegende Regel besagt, dass eine schneller drehende Schleifscheibe zu kürzeren Kontaktzeiten zwischen Schleifscheibe und Werkstück führt. Dies kann in bestimmten Fällen zu einer Reduzierung von Schleifbrand beitragen, vorausgesetzt, der Prozess ist für hohe Geschwindigkeiten mit entsprechender Kühlleistung konzipiert. Eine erhöhte Umfangsgeschwindigkeit kann jedoch auch dazu führen, dass die Schleifscheibe zu hart wirkt und somit zu Schleifbrand neigt. Ein tiefgehendes Verständnis des Schleifprozesses ist daher essenziell. Oft lässt sich das Risiko von Schleifbrand durch eine Verringerung der Umfangsgeschwindigkeit vc der Schleifscheibe minimieren. Zusätzliche Parameter - wenn zu hoch oder zu tief gewählt - die beim Rundschleifen einen Einfluss auf den Schleifbrand ausüben, umfassen die Werkstückdrehzahl pro Minute nw, die Zustellung im Einstechverfahren vf in Millimetern pro Minute. Beim Aussenrund-Längsschleifen umfasst dies die Parameter Zustellung ae in Millimetern pro Überlauf sowie den Längsvorschub vfa in Millimetern pro Minute.
Beim Flach- oder Tiefschleifen sind die Tischgeschwindigkeit in m/min vw und die Tiefenzustellung ae pro Überlauf in mm weitere wichtige Kenngrössen. Ein bewährter Kennwert ist das Geschwindigkeitsverhältnis qs zwischen Schleifscheibe und Werkstück. Beim Rund- und Flachpendelschleifen liegt dieses zwischen 60 und 80 und sollte 120 nicht überschreiten, da über diesem Wert die Brandgefahr ansteigt. Ein Geschwindigkeitsverhältnis qs von 80 bedeutet, dass die Umfangsgeschwindigkeit der Schleifscheibe 80-mal höher ist als die des Werkstückes. Beim Tiefschleifen sollte das Geschwindigkeitsverhältnis qs mindesten über 1000 liegen, idealerweise aber bei 1500 beginnen, um aus der Schleifbrandgefahrenzone zu gelangen.
2. Kühlschmierzuführung und Düsenauslegung
Die Austrittsgeschwindigkeit des Kühlschmierstoffes Vkss sollte idealerweise der Umfangsgeschwindigkeit der Schleifscheibe vc entsprechen. Dies ist bekannt unter dem Begriff Gleichlaufschmierung. Sowohl niedrigere als auch höhere Austrittsgeschwindigkeiten können das Risiko für Schleifbrand signifikant erhöhen. Die Positionierung der Düse ist so zu wählen, dass der Kühlmittelstrahl tangential zum Umfang der Schleifscheibe, kurz vor der Kontaktzone zwischen Schleifscheibe und Werkstück, auftrifft. Ein Anstellwinkel von 20° hat sich dabei in der Praxis als effektiv erwiesen. Zudem sollte die Düsenöffnung keine Rundungen oder Beschädigungen aufweisen, die den Strahl durch Verwirbelung mit Luft beim Austritt beeinträchtigen könnten. Der Einsatz von 3D-gedruckten Stahldüsen wird heutzutage empfohlen , die über IRPD bezogen werden können. Für die Abschätzung des erforderlichen Kühlschmierstoff-Volumenstroms gilt die Richtlinie: Qkss = ca. 1.5 – 5.0 l/min pro mm der im Einsatz befindlichen Scheibenbreite. (Nach Angaben von Prof. Dr. Bernhard Karpuschewski vom IWT Bremen).
3. Abrichtparameter
Die Praxis hat gezeigt, dass falsch gewählte Abrichtparameter oft Ursache von Schleifbrand sind, insbesondere, wenn die Schleifscheibe zu fein abgerichtet wurde. Eine zu fein abgerichtete Schleifscheibe erhöht den Schleifdruck und die Kornreibung, was zwangsläufig zu höherer Prozesswärme führt. Es gibt einfache Formeln zu Berechnung des Abrichtvorschubes vd von stehenden Abrichtwerkzeugen. Man wählt einen Überdeckungsgrad ud von 4, bestimmt die Wirkbreite bd (bei einer Fliese meist bei ca. 0.8 mm) und bringt folgende Formel zur Anwendung:
vd (Abrichtvorschub in mm/Min) = (ns (Scheibendrehzahl/Min) x bd (Wirkbreite des Diamanten in mm) ) / ud (Überdeckungsgrad)
Um eine hervorragende Oberflächengüte und zugleich hohe Abtragsraten zu erzielen, ist es von grösster Bedeutung, mit kleinen Zustellungen ad (Schnitttiefen), d.h. 0,002 bis 0,03 mm pro Abrichtdurchgang zu arbeiten. Um die Oberflächenrauheit und die Schnittigkeit der Scheibe zu erhöhen, wird die Abrichtvorschub vd und nicht die Tiefe der Abrichtzustellung ad erhöht. Bei rotierenden Abrichtwerkzeugen ist ein Geschwindigkeitsverhältnis qd von 0.6 bis 0.8 im Gleichlauf zu wählen. Dies ergibt eine schnittige Schleifscheibe von geringerer Brandneigung.
qd (Geschwindigkeitsverhältnis) = VR (Umfangsgeschwindigkeit der Diamantrolle) / VC (Umfangsgeschwindigkeit der Schleifscheibe)
4. Schleifscheibenspezifikation
Falsch gewählte Schleifscheibenspezifikationen können ebenfalls eine Schleifbrandursache darstellen. Je feiner das Schleifkorn, desto höher wird der Schleifdruck und auch die Wärmeeinbringung ins Werkstück. Schleifscheiben von einem hohen Härtegrad bedeuten hohe Bindungsanteile, die die Brandneigung erhöhen, da Bindung bekanntlich nicht schleift und Reibung verursacht. Enge Strukturen weisen wenig Porenraum auf, der nur geringe Mengen an Kühlschmierstoff in die Schleifzone bringt und auch die Späne nicht effizient abführen kann. Hier sollte der Anwender mit seinem Scheibenlieferanten Rücksprache nehmen. Insbesondere beim Tiefschleifen kommen hochporöse und weiche, bindungsarme Spezifikation zum Einsatz, ansonsten ist Schleifbrand vorprogrammiert. Auch beim Aussenrund-Schrägeinstechen sollten bei Schulterhöhen über 7 mm, poröse Schleifscheiben zum Einsatz kommen.
5. Fachkräftemangel oder fehlendes Schleifwissen
Die vier ersterwähnten Punkte und deren Zusammenhänge müssen von den Maschinenbedienern verstanden werden. Sollte dies nicht der Fall sein, stehen wir Ihnen gerne mit dem Angebot entsprechender Schleifkurse zur Seite.
Methoden der Schleifbrandprüfung
- Sichtprüfung
Das Werkstück kann mit dem blossen Auge betrachtet werden, um zu sehen, ob Verfärbungen auf der Werkstückoberfläche aufgetreten sind. Diese Methode ist nicht sehr zuverlässig, da Schleifbrand möglicherweise beim Schruppen entstand und Verfärbungen vom Schlichten entfernt werden.
- Nital-Ätzen
Das Nital-Ätzen ist ein mehrstufiger, zerstörungsfreier Prozess für gehärtete Stähle. Dieses Verfahren kann nicht für Luftfahrtteile aus Inconel und dergleichen Materialien verwendet werden. Durch Ätzen mit verdünnter Salpetersäure und Bleichen mit verdünnter Salzsäure kann Schleifbrand als veränderte Graufarbtöne sichtbar gemacht werden.
- Barkhausen Verfahren
Die Barkhausenrauschen-Prüfung, ein elektromagnetisches Verfahren, erkennt durch Schleifbrand hervorgerufene Härte- und Eigenspannungsunterschiede in ferromagnetischen Werkstoffen. Das Barkhausen-Verfahren ist völlig zerstörungsfrei und kann unmittelbar an der Schleifmaschine eingesetzt werden. Das Verfahren benötigt aber eine Eichung mit einem schleifbrandfreien Werkstück.
- Röntgendiffraktion (XRD)
Dieses Verfahren ermöglicht das Messen von Materialeigenspannungen auch in Nichteisenmetallen wie Inconel und andere schwerschleifbaren Nickellegierungen der Raum- und Luftfahrt.
Haben Sie Fragen?
Wenn Sie zu diesem Thema weiterführende Fragen haben, sprechen Sie uns an. Unsere Experten stehen Ihnen mit Rat und Tat zur Seite.
Beispiel von Schleifbrand
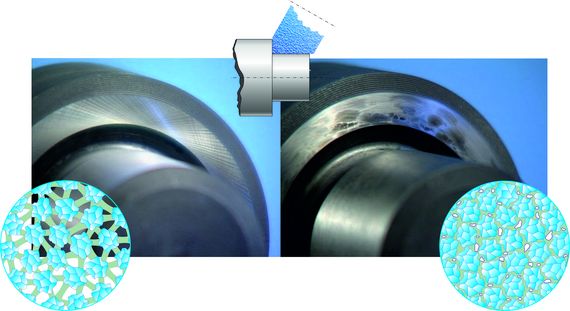
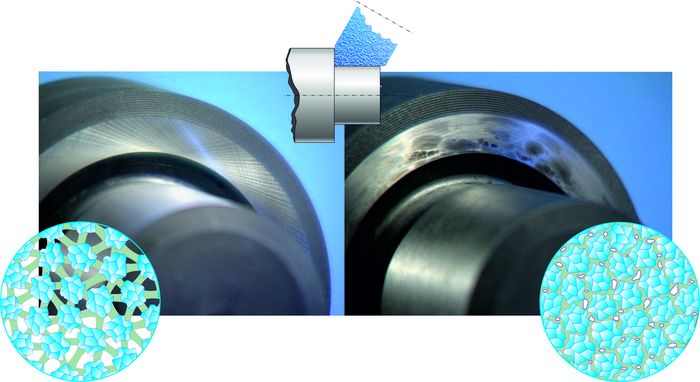
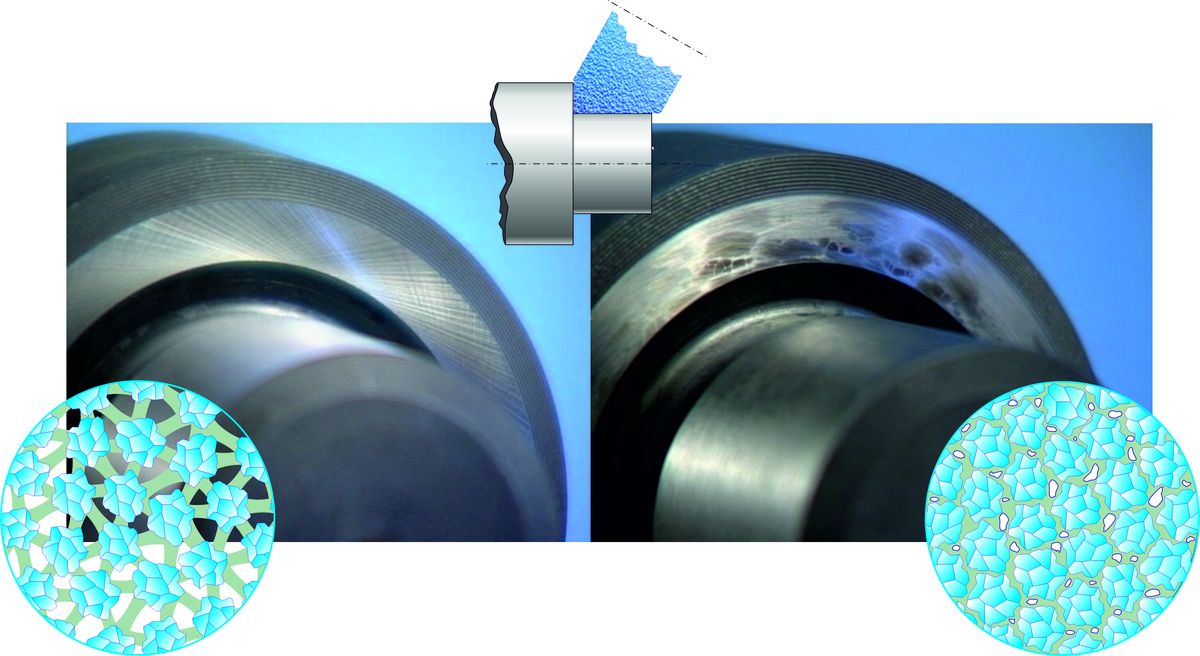
Rechts: Schleifbrand; Verwendung einer geschlossenen Schleifscheibe