研削焼けの回避
研削工程で過度の熱が発生すると、ワークが熱損傷する可能性があり、その結果、影響を受けた部品がスクラップになってしまいます。このモーションブログでは、この熱の発生原因とその確認方法、どのようにそれを回避するかを取り上げています。
研削焼けの定義
まず、研削焼けの定義とその原因から始めましょう。焼入れ鋼を研削する場合では、研削スピンドルによって加えられるエネルギーのほぼすべてが熱に変換されます。理想的な研削プロセスでは、この熱は、発生する切り屑とクーラント液によって放熱される必要があります。ただし、熱を効果的に放散できない場合、熱がワークに浸透し、研削焼けや熱損傷と呼ばれる組織または粒界の変化を引き起こす可能性があります。これらの変化は、研削割れや引張応力を促し、それが確認された場合、必然的に該当する部品はスクラップになる可能性があります。これは、モーター、タービン、機械といった重要な用途の部品において、欠陥によって生じる可能性のある、深刻な事態を回避するために必要です。
研削焼けの発生
研削焼けは、さまざまな要因に影響される複雑な現象です。研削焼けが起こらないようにするには、適切な研削砥石の使用、効果的な冷却、材料特性の理解、研削盤の制御、専門的な研削技術の活用と同様に、研削パラメータの正しい選択が重要です。これらの要因を注意深く観察し、適切に調整することで、研削結果の品質を向上させ、研削による損傷リスクを軽減できます。
以下では、主な 原因 について説明します。
1. 研削パラメータ
すべての研削工程において、メートル/秒で表される研削砥石の周速度 vc は、最も重要な研削パラメータの1つです。基本的な法則として、砥石の回転速度が速いほど、砥石とワークの接触時間は短くなります。高速回転用に設計され、それに見合った冷却能力があれば、研削焼けの軽減に役立ちます。しかし、周速が速くなると砥石が硬く作用しすぎて、研削焼けが発生しやすくなることがあります。そのため、研削プロセスを深く理解することが不可欠になります。多くの場合、研削砥石の周速度 vc を下げることで、研削焼けのリスクを最小限に抑えることができます。円筒研削中の研削焼けに影響を及ぼす追加パラメータ(高すぎるまたは低すぎる場合)には、1分あたりのワーク回転数 nw、プランジ研削での送り速度vf(ミリメートル/分)があります。外面円筒トラバース研削の場合、ワンパスあたりのミリメートル単位の切込み量 aeとトラバース送り速度 vfa(ミリメートル/分)が含まれます。
平面研削またはクリープフィード研削では、テーブル速度(m/min) vw とワンパスごとの切込み深さ aeも重要なパラメータとなります。実証済みの特性値としては、砥石とワークの速度比 qs があります。円筒研削および平面トラバース研削の場合、これは60から80 の間であり、120を超えてはならない。この値を超えると発火の危険性が高まります。速度比 qsが80とは、砥石の周速がワークの周速の80倍を意味します。クリープフィード研削の場合、速度比 qsは少なくとも1000を超える必要がありますが、理想的には1500から始めると、研削焼けの危険ゾーンから離れることができます。
2. クーラント液の供給およびノズル設計
クーラント液の出口速度 Vkssは、理想的には研削砥石の周速 vc 相当になる必要があります。これは同期潤滑と呼ばれています。出口速度が低い場合も高い場合も、研削焼けのリスクが大幅に増加する可能性があります。ノズルは、クーラント液が研削砥石とワークの間の接触領域の直前で研削砥石の円周に接線方向に当たるように位置決めしてください。20°の迎角が有効であることが実際に証明されています。さらに、ノズル開口部には、噴出し時に空気の乱流によって噴射に影響を及ぼすような丸みや損傷があってはなりません。現在では、IRPDから入手できる3次元造形された金属製ノズルの使用が推奨されています。必要なクーラント流量の推定には、以下のガイドラインが適用されます:Qkss = 使用砥石幅 1mm あたり約1.5 ~ 5.0 l/min。(IWTブレーメンのBernhard Karpuschewski教授による)
3. ドレッシングパラメータ
経験上、ドレッシングパラメータの選択が間違っていることが(特に研削砥石が微細にドレッシングされた場合)、研削焼けの原因となることがよくあります。研削砥石のドレッシングが細かすぎると、研削圧力と砥粒摩擦が増加し、必然的に加工熱が上昇します。固定ドレスの場合、ドレッシング送り vd を計算するための簡単な公式があります。オーバーラップ係数 udを4とし、有効幅 bd(フリーゼの場合、通常は約 0.8 mm)を決定し、次の公式を適用します。
Vdd (ドレッシング送り速度(mm/min)= (ns (砥石回転数/min)x bd (ダイヤモンドの有効幅(mm)) / ud (オーバーラップ係数)
優れた表面品質と高い除去率を同時に達成するには、ドレッシングパスあたり 0.002~0.03mmの少ない切込み量 ad(切込み深さ)で作業することが非常に重要です。砥石の表面粗さと研削能率を高めるためには、ドレッシング送りの深さ adではなく、ドレッシング送り速度 vdを大きくします。ロータリードレッサの場合、同期回転で速度比 qd を0.6~0.8にする必要があります。これにより、焼けが少なく切れ味の良い砥石になります。
qd(速度比)= VR(ダイヤモンドロールの周速)/ VC(砥石の周速)
4. 砥石の仕様
研削砥石の仕様が正しく選択されていない場合も、研削焼けの原因となる可能性があります。砥粒が細かいほど、研削圧力が高くなり、ワークへの入熱が大きくなります。高硬度の砥石はボンドの割合が高いことを意味し、ボンドが研削を行わず摩擦を引き起こすことがよく知られているように、研削焼けの傾向が高まります。細かい構造にはが気孔ほとんどないため、研削ゾーンに少量のクーラント液しか入り込めず、切粉を効率的に排出できません。砥石の詳細については、砥石の各サプライヤーにご相談ください。特にクリープフィード研削では、多孔質で柔らかく、結合度の低い仕様のものが使用されます。そうしないと、研削焼けが避けられません。外面のプランジ研削でも、ショルダー高さが7mmを超える場合、多孔質研削砥石を使用してください。
5. ベテランの不足、または研削専門技術に関する知識の欠如
機械オペレーターは、上記に述べた4つのポイントとその関連性を理解している必要があります。そうでない場合は、適切な研削トレーニングコースを提案させていただきます。
研削焼けの確認方法
- 目視点検
ワークを肉眼で観察して、ワークの表面に変色がないかで確認することができます。この方法は粗加工時に研削焼けが発生し、仕上げ加工で変色が除去されるため、あまり信頼性が高くありません。
- ナイタールエッチング
ナイタールエッチングは、焼入れ鋼の多段階の非破壊プロセスです。この方法は、インコネルや類似の材料で作られた航空部品には使用できません。希硝酸によるエッチングと希塩酸による漂白により、研削焼けをグレーの変色として可視化できます。
- バルクハウゼンノイズ法
電磁的方法であるバルクハウゼンノイズ法は、研削焼けによって生じる強磁性材料の硬度と残留応力の違いを検出します。バルクハウゼンノイズ法は完全に非破壊的で、研削盤上で直接使用できます。ただし、この方法では、研削焼けのないワークでキャリブレーションが必要となります。
- X線回折(XRD)
この方法では、インコネルや航空宇宙産業で使用されるその他の研削が困難なニッケル合金などの非鉄金属であっても、材料の内部応力を測定できます。
ご質問がありますか?
これらのトピックに関するご質問は、当社までお問い合わせください。当社のエキスパートがアドバイスとサポートを提供します。
研削焼けの例
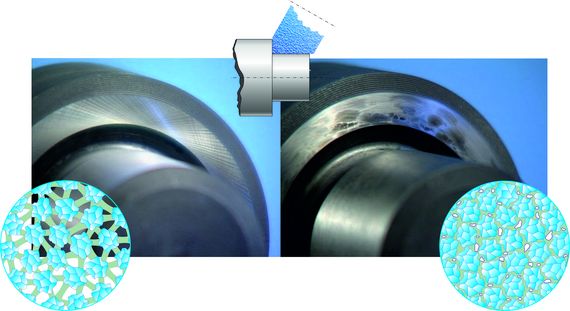
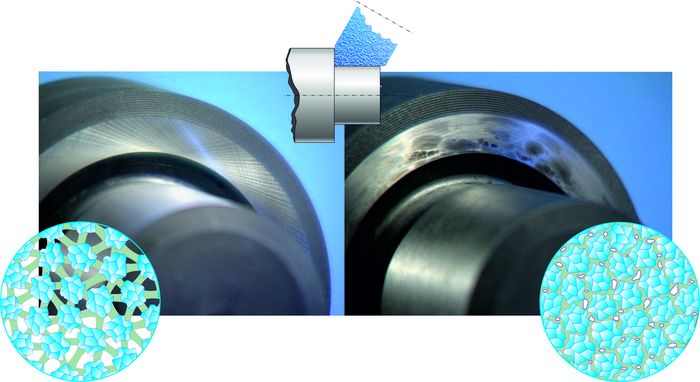
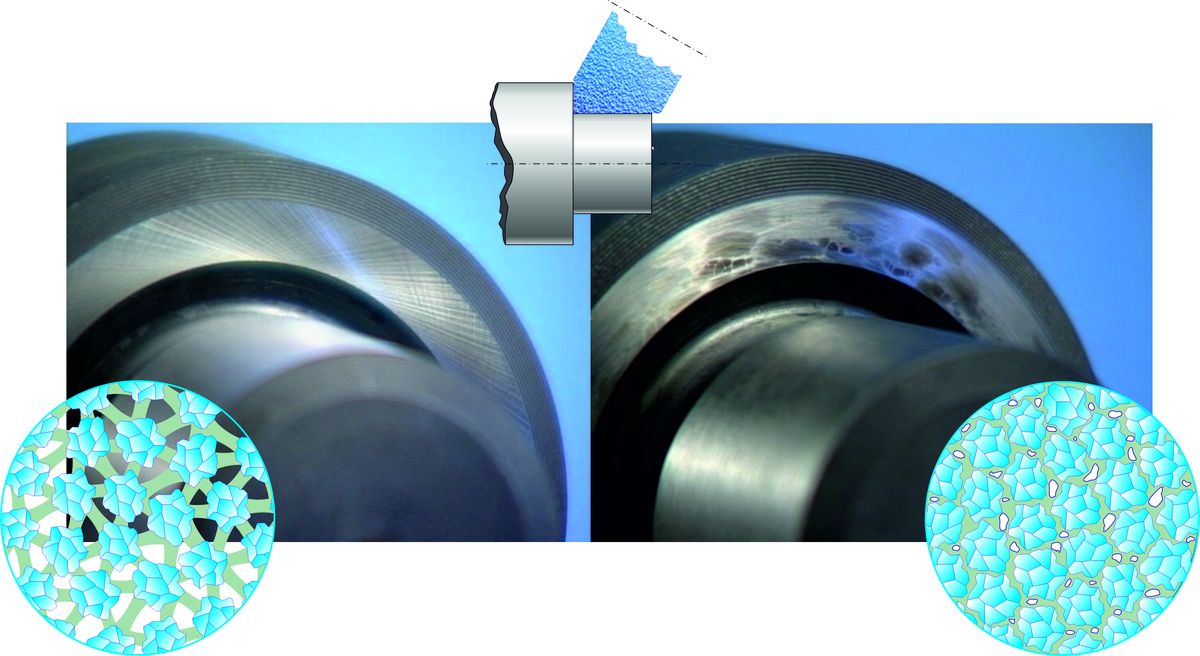
右:研削焼けあり、組織が密な砥石を使用