Differences Between Creep Feed Grinding and Conventional Traverse Grinding Easily Explained
Grinding Process
The chip thickness and therefore the cutting force on the single grain are lower with creep feed grinding than with conventional traverse grinding. There are no recurring impact loads on the grinding wheel so that the abrasive grains can be held by the bond matrix longer before the grains break out. On the other hand, the thermal load and the total cutting forces are higher.
In creep feed grinding, the higher cutting forces require significantly higher static and dynamic rigidity and higher drive performance of the grinding machine than in conventional traverse grinding. The high thermal load during creep feed grinding not only represents a high load on the tool and grinding machine, but it can also damage the workpiece material and can lead to cracks and structural changes. Such structural changes do not occur, or only occur to a limited degree during conventional traverse grinding and are removed by the subsequent pass.
During conventional traverse grinding, the contact surface of the tool and the workpiece can be easily supplied with cooling lubricant due to the short length of the contact area. Creep-feed grinding requires the cooling of a much larger contact surface and the dissipation of more heat due to the higher friction. Therefore, the cooling lubricant must be supplied at high pressure and high flow rates through nozzles and supply lines with defined shapes.
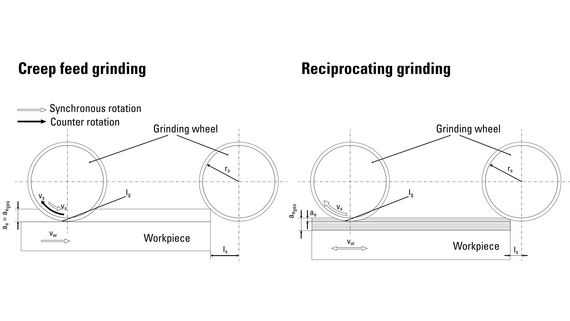
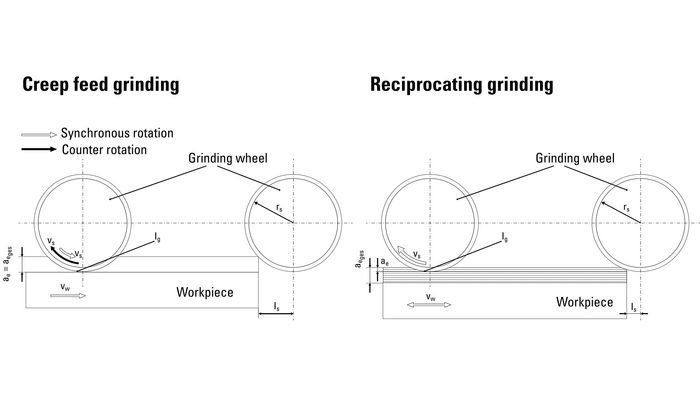
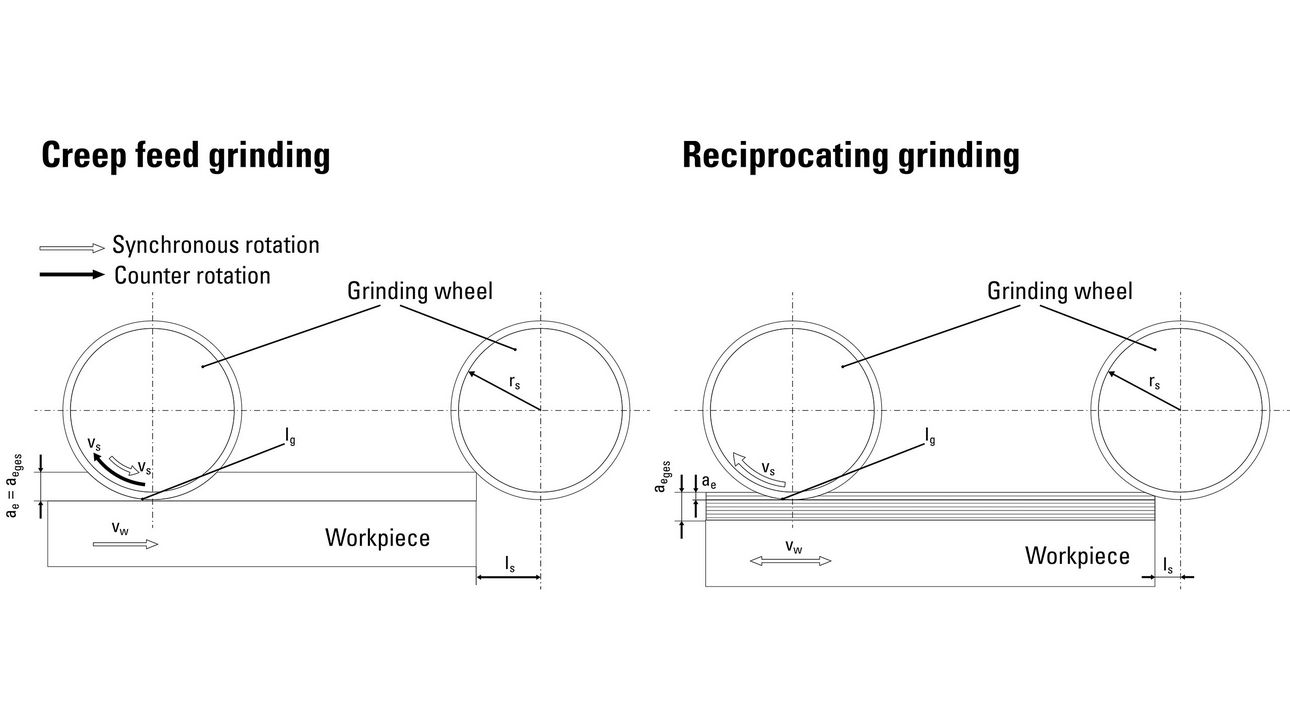
Conventional traverse grinding | Creep feed grinding | |
Feedrate | high | low |
Infeed | low | high |
Number of passes | many | 1 (or less) |
Co- and counter-rotating wheels | alternating | selectable |
Non-productive times | high | low |
Average chip thickness | higher | lower |
Average chip length | lower | higher |
Average contact temperature | lower | higher |
Grinding forces | lower | higher |
Surface quality | coarser | finer |
Wheel wear | higher | lower |
Tendency for chatter | higher | lower |
Grinding Results
In creep feed grinding, the surface roughness is significantly finer than in conventional traverse grinding due to the higher number of abrasive grains in contact and also due to smaller feed rates. Since the functional surface properties of a workpiece are often important, creep feed grinding has an advantage here. This can be traced back to the kinematics of creep feed grinding. The abrasive grains that do not break out from the bond, due either to their position in the bond or due to advanced wear , contribute due to plastic deformation, to the smoothing of the workpiece surface. On the other hand, there are higher forces and thermal stresses, which require a significantly higher static and dynamic rigidity of the grinding machine.
In conventional traverse grinding, the number of cutting edges involved in the machining process is higher in relation to the material volume. A coarser surface is created due to the short contact time between the grain and workpiece. Unlike in creep feed grinding, the surface irregularities on the workpiece are not smoothed out by the adjacent cutting edges engaging at the same time but are displaced by subsequent grinding strokes. This leads to a temporary blanketing by displaced material. These surface irregularities also increase the surface roughness. Due to the stress during the process, these surface irregularities also do not correspond to the base material, and there is no material cohesion as in the original state. As a result, there is an increased risk that, for example, in plain bearing surfaces which are often machined by grinding, that particles will detach from the surface in later use and lead to component failure due to friction and crushing.
Grinding Wheels
The choice of abrasive mainly depends on the properties of the workpiece material and the conditions of the grinding process, for example, the use of cooling lubricant. The higher grinding forces and thermal stresses in the work zone during creep feed grinding require an adaption of the grinding wheel specification.
With conventional traverse grinding, the wheel must absorb the impact stress caused by the alternating co- and counter-rotation and by the high grinding forces on the single grain. With creep feed grinding, the impact and single grain forces are lower, and high thermal stresses must be absorbed in the work zone.
Another aspect that influences the wheel choice is the chip shape, which is decisively influenced by the workpiece material. With creep feed grinding, the chips are relatively thin and long. In contrast, conventional traverse grinding usually produces short, thick chips. The combination of abrasive grain/bond must be selected in such a way that the chips can be easily removed from the work zone during creep feed grinding. Therefore, there must be sufficient chip space. An open wheel structure allows a higher heat dissipation through the coolant in the pores, which is especially important in creep feed grinding.
Conclusion
In practice, both processes have proven themselves and are justifiable. With the MÄGERLE, BLOHM and JUNG range, we offer machines for both processes.