Mounting and Balancing Grinding Wheels
Picking the correct grinding wheel type is not the only factor that influences grinding results. Proper mounting and balancing of the grinding wheels is also essential.
Mounting of Grinding Wheels
The mounting procedure depends on the grinding wheel type. The procedures for aluminum oxide, CBN and diamond grinding wheels are explained below.
Mounting Aluminum Oxide Grinding Wheels
- Visual inspection of the grinding wheel and checking the permissible number of revolutions or circumferential speed.
- Performing a clank test to check whether the grinding wheel has a crack: Light tapping of the grinding wheel with a non-metallic hammer. If a clear ringing can be heard, then the wheel is ok.
- Place plastic blotters between flange and grinding wheel to compensate for grain peaks and unevenness. Alternatively, cardboard blotters can be used, these should be moistened on both sides with oil or coolant. Blotters should only be used once.
- Oil the flange.
- Mount the grinding wheel onto the flange: The clamping surfaces must be clean and flat and the grinding wheel should slide on easily.
- Tighten the flange bolts evenly diagonally across the flange with a torque wrench.
Mounting of CBN and Diamond Grinding Wheels
- The procedure is similar to that for aluminum oxide grinding wheels. No ring-test or plastic blotters are necessary for metallic or resin-based wheel bodies.
- Tighten the mounting screws only slightly so that the wheel can be moved with a light tap.
- Mount the grinding wheel on the machine.
- Check the runout with a dial gauge, if necessary correct with a plastic hammer (runout < 0.02 mm). When checking the runout on the abrasive surface, a measuring device with a stylus roller should be used to avoid wear on the probe.
- Tighten the flange bolts evenly and diagonally across the flange with a torque wrench and check the runout.
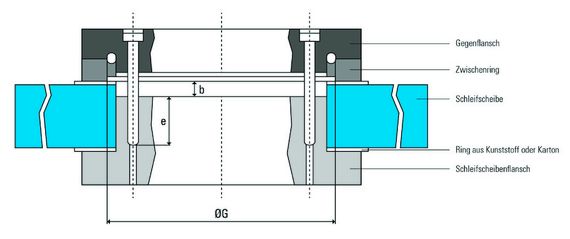
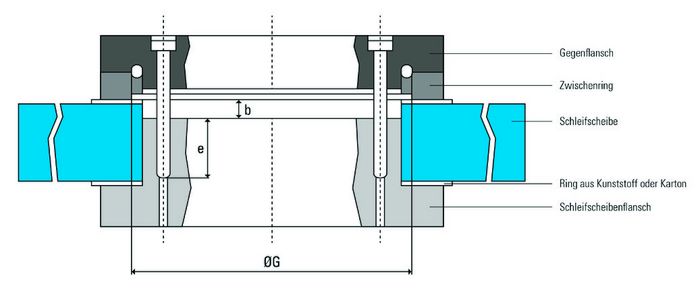
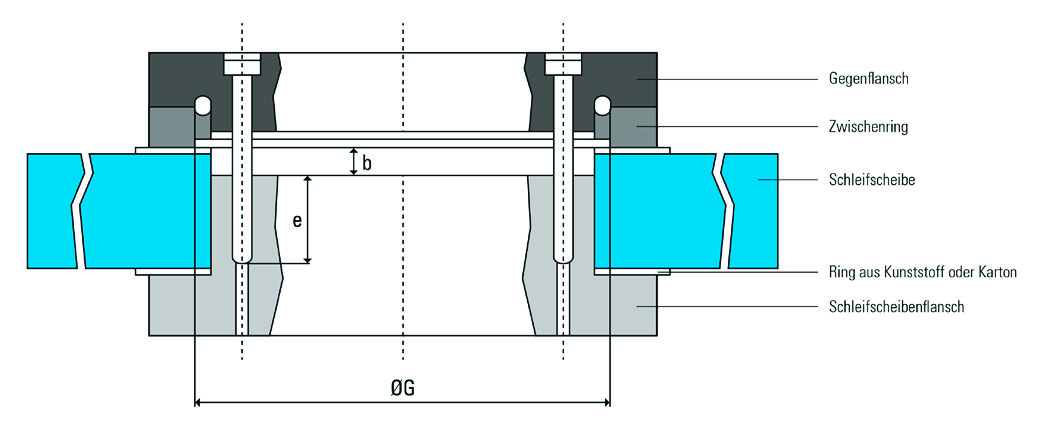
The screw-in depth (e ≥ 1.5 x thread diameter
of the grinding wheel flange) is a standardized value (FEPA) and must not be changed.
Note: The grinding wheel must be properly clamped (distance b). If necessary, a distance ring must be mounted between the grinding wheel and counter flange. The flange and the distance ring must be relieved to the same diameter (G), otherwise the grinding wheel can be sheared off.
Balancing of Grinding Wheels
The different grinding wheel types are balanced identically. There are two balancing methods: Static and dynamic balancing.
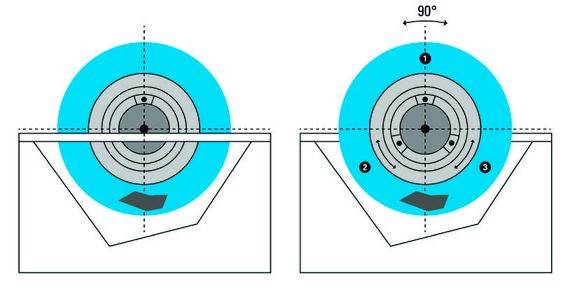
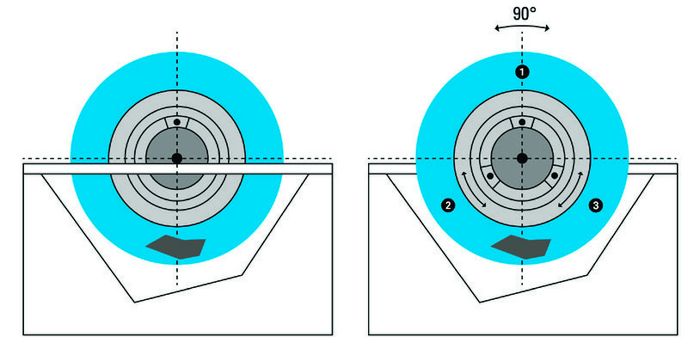
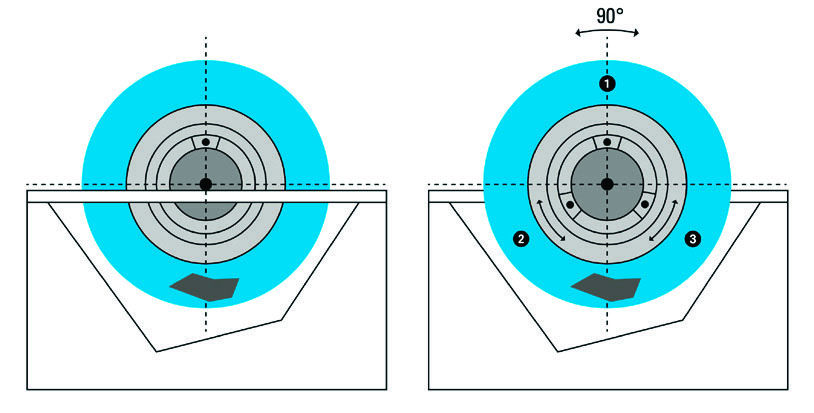
Static Balancing (Outside the Machine)
Static balancing of grinding wheels is performed where there is no balancing unit on the machine. In such situations balancing is performed outside the machine on a balancing stand. The balancing process is performed with the grinding wheel at rest.
Balancing stand
A spirit level must be used to level the balancing stand and the grinding wheel must be dry. The balancing arbor, its seat, and also the contact surface must be clean. In addition, the balancing stand must be placed on a firm base (no rubber pads).
Procedure
- Remove all balancing weights.
- Set the grinding wheel on the balancing stand and let it settle.
- The heaviest point of the wheel is now located at the bottom. Weight no. 1 is mounted exactly where the heaviest point of the wheel is and will not be moved.
- Arrange the two other weights, no. 2 and no. 3, symmetrically at approx. 120°.
- Now the grinding wheel is rotated by 90° and stopped. If weight no. 1 pulls downward, move the two other weights symmetrically away from no. 1. In case of the opposite, move the two other weights toward no. 1.
Advantages
- Cost-effective
Disadvantages
- Grinding wheel must be removed from the machine for balancing
- This method is less precise than dynamic balancing
Dynamic Balancing (Inside Machine)
Dynamic balancing takes place inside the machine with a rotating grinding wheel. Two variants of dynamic balancing are described below.
Manualbalancing (pre-balancing)
A unit is required that is either permanently installed in the machine and can be operated via the control or used as an external instrument.
- The grinding wheel is mounted in the machine. No prior static balancing is required.
- Two balancing weights are manually mounted to the flange in a neutral position (e.g. 0° and 180°).
- With the wheel running, an initial measurement cycle is initiated to detect imbalance and phase.
- One of the weights is then adjusted by a defined angle (e.g. 30°) and a second measurement is initiated.
- Based on these two measurements, the unit determines where the balancing weights must be mounted.
Advantages
- Fast and accurate method
- Cost-effective
- Balancing possible at any time without removing the grinding wheel from the machine
- Up to 4 grinding wheels can be balanced in one machine with one unit
- 2-plane balancing (for 2 wheels on one spindle) is possible
- No wear parts
Disadvantages
- Balancing weights must be positioned manually
Automatic balancing
This requires a balancing head and a balancing unit, both of which are permanently installed in the machine.
- The balancing head is integrated behind the grinding wheel in the grinding spindle.
- The balancing procedure (balance check, balancing where necessary) is started via the machine control.
- The unit determines the imbalance and controls the balancing head.
- The balancing head uses a motor to move the weights to the specified positions.
Benefits
- No manual adjustment is necessary
- The balance check is started automatically when the grinding wheel is switched on. Balancing is carried out only if it is necessary
- The grinding wheel is automatically checked periodically for balance and re-balanced if necessary
Disadvantages
- Costly method
- The balancing head will not work with two grinding wheels mounted on one spindle
- 2-plane balancing is not possible
- The balancing cycle takes a long time (balancing process is a trial and error procedure and is carried out until the desired balancing quality is achieved)
- More susceptible to interference than for example pre-balancing (influenced by external vibrations)
- The balancing head can be subject to wear and may need to be overhauled or replaced
Interested in More?
Want to know more about wheel mounting and balancing? The experts from UNITED GRINDING will be happy to support you!