The new S33 – The productive for Individual Requirements
Universal and flexible. These are the features of the new S33, the CNC universal cylindrical grinding machine from STUDER. It can grind small to large workpieces in single batch, small or large series and is available with centre distances of 400 mm (15,7") / 650 mm (25.6") / 1000 mm (40") / 1600 mm (63") and a centre height of 175 mm (6.9"). The changeover from grinding between centers to live spindle grinding takes place in record time. Complex workpieces are easily ground in just one clamping.
The basis for the universal cylindrical grinding machine S33 is the machine bed made of solid Granitan® S103. Thanks to its favorable thermal behavior this offers a high degree of dimensional stability, short-term temperature fluctuations are largely compensated for by the mineral casting. STUDER has redesigned the machine base geometry and supplemented it with an innovative machine base temperature control. This ensures a fast and stable production. The mounting of the dressing unit on the double T-slot of the longitudinal slide massively reduces the time needed for setup or changeover of the machine.
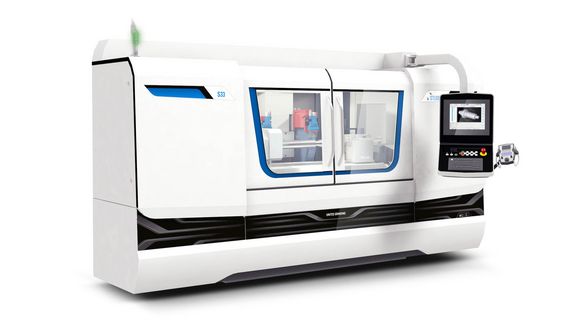
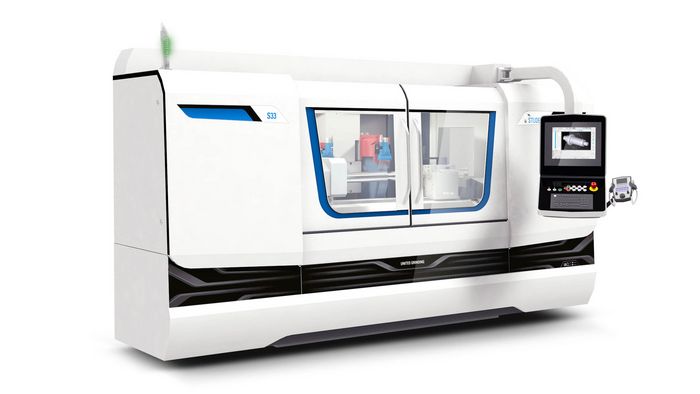
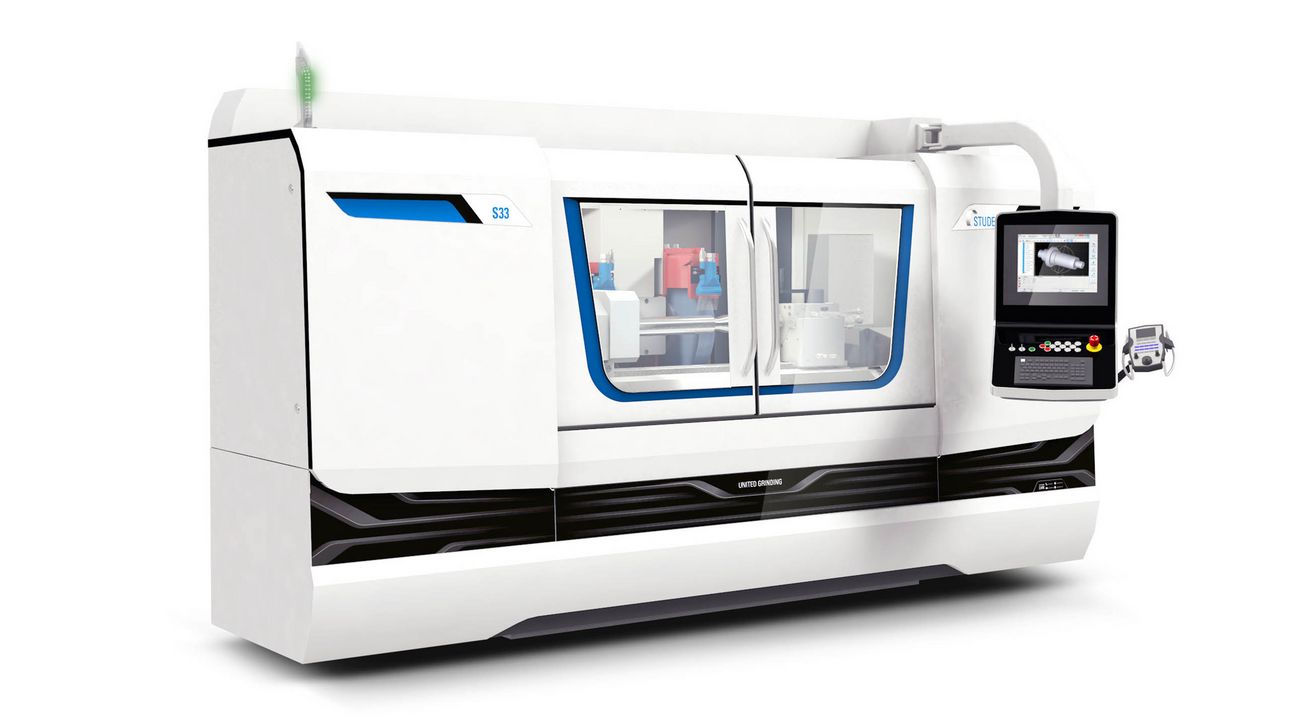
A wide range of wheelhead configurations.
The S33 is based on the STUDER T-Slide concept. It now has an extended X-axis stroke of 370 mm (14.5") STUDER offers various wheelhead versions. The turret wheelhead with a 1° Hirth coupling and automatic swivel, can accommodate up to two external and one internal grinding spindle and is also equipped with the latest generation of contact detection. The external wheelhead with a grinding wheel right, can be manually set to 0° / 15° / 30° The machine setup and changeover costs can be reduced thanks to the turret wheelhead with multiple grinding wheels and the fast setup software Quick-Set. The S33 can easily handle internal-, external- and face grinding in one clamping which leads to an even higher efficiency in complete machining. The C-Axis, with an option of either a direct or indirect measuring system, allows the grinding of forms and threads. The S33 can also be equipped with a chuck workhead specially designed for grinding chuck parts.
Convincing software
More than a hundred years of grinding experience is integrated in StuderWIN, which enables safe programming and efficient use. StuderTechnology requires just a few parameters to automatically calculate precise grinding parameters in just seconds. Good quality is assured from the start, as is a stable process right from the beginning. The optional integrated modules such as StuderForm, StuderThread or StuderContourBasic extend the functionality of the machine. The hand-control device PCU makes it possible to set up the machine close to the grinding process. With electronic contact detection, downtimes can be reduced to a minimum. With the standardized loader interface, the S33 can also be automated.
Benefits at a glance
- Distance between centres 400 mm (15.7") / 650 mm (25.6") / 1000 mm (40") / 1600 mm (63").
- Centre height 175 mm (6.9")
- Maximum workpiece weight 150 kg (330 lbs)
- Thermal stability through innovative machine base cooling (CD 400 mm 650 mm (25.6") to 1600 mm (63")
- Double T-Slot for dressing devices
- Numerous wheelhead variants
- Motor spindle incl. frequency convertor for turret wheelhead
- Constant cutting speed as standard
- Software StuderWin with StuderTechnology
- Reduced setup and resetting times with STUDER Quick-Set
- Flexibly expandable with integrated software modules
- Can be easily automated