How to improve the efficiency of your cylindrical grinding machines
STUDER, the specialist for cylindrical grinding machines within UNITED GRINDING Group, manufactures some of the most precise, reliable, and efficient machines in the world. Read this article to find out how you can boost the performance of your cylindrical grinding machine even further.
1. Retrofitting with automatic loading systems
For companies processing many different workpieces in small series, fully automatic robot loading systems that are designed for high quantities usually make little sense. For this reason, STUDER has developed the STUDER uniLoad for universal external cylindrical grinding machines and the STUDER roboLoad for internal cylindrical grinding machines to machine radii. Both systems offer standard automation for a wide range of parts and allow for a quick setup and resetting in less than 15 minutes.
uniLoad can be easily retrofitted on the following STUDER machine models: favorit, S33, S31; roboLoad is suitable for retrofitting on the following machines: S121 Radius,S131 Radius,S141 Radius.
2. LaserControl
Increasing efficiency in the grinding process is primarily about saving time. To achieve this goal, STUDER goes beyond simply loading and unloading workpieces when it comes to automation. The reason for this is that other common processes can also be automated and simplified.
LaserControl is an example of this. It is a synonym for laser process measurement technology directly integrated into the machine, which enables you to measure your workpieces in the clamped state. This makes sure that the workpieces are within tolerance at the end of the grinding cycle. And this is done without manual intervention and without having to unclamp the workpiece. Above all, this saves time and also reduces the susceptibility to errors.
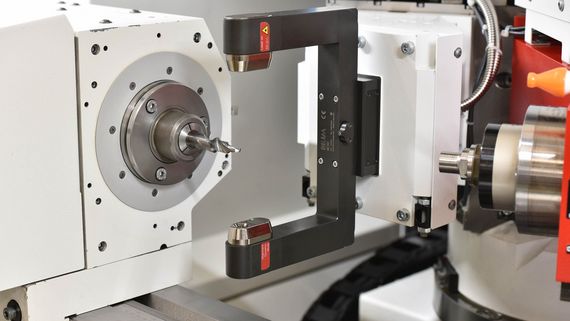
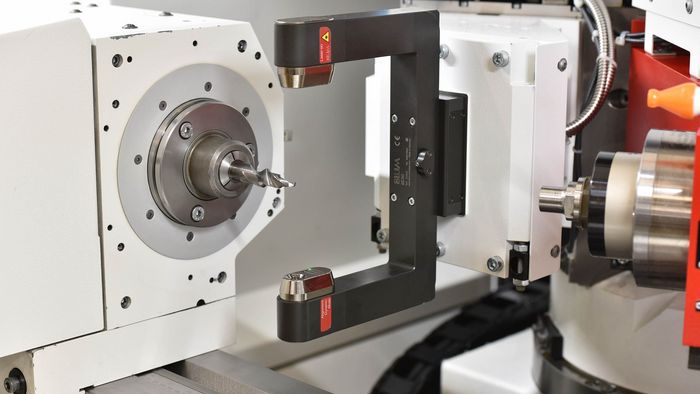
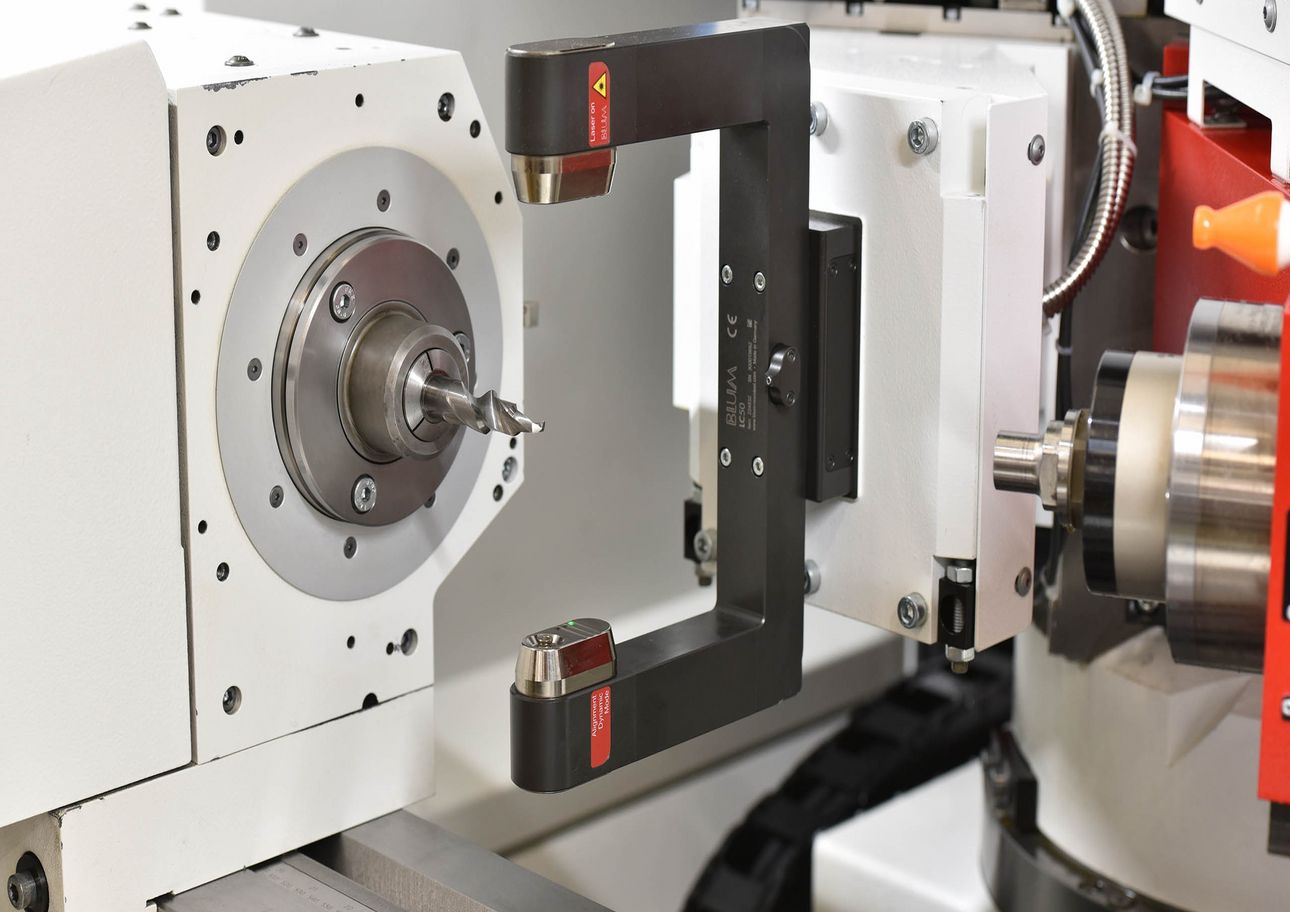
3. SmartJet® and Smart Cooling
When it comes to automated process efficiency, we must also mention the Smart Cooling concept featuring SmartJet® nozzles. These enable an accurately positioned and machine-controlled coolant flow to the grinding wheel. This accurate and durable method takes little time to convert and provides a constant coolant flow to the grinding wheel cutting zone The consequences are optimal positioning and utilization of the coolant without the need for manual re-adjustment during each machine setup.
4. Synchronous tailstock
Another valuable tip to boost efficiency: By decreasing the number of clamping steps per part, you can machine more workpieces in the same amount of time. Thanks to the synchronous tailstock from STUDER, you can grind the entire length of a workpiece in a single clamping. This brings additional flexibility and productivity to the process.
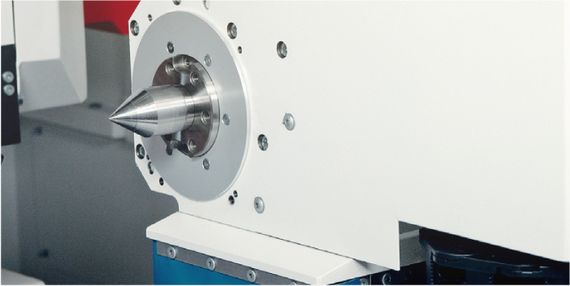
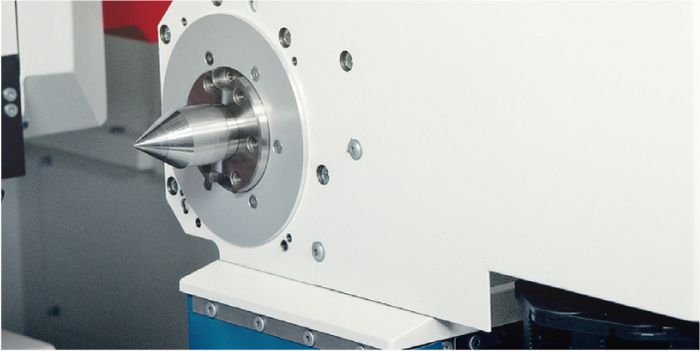
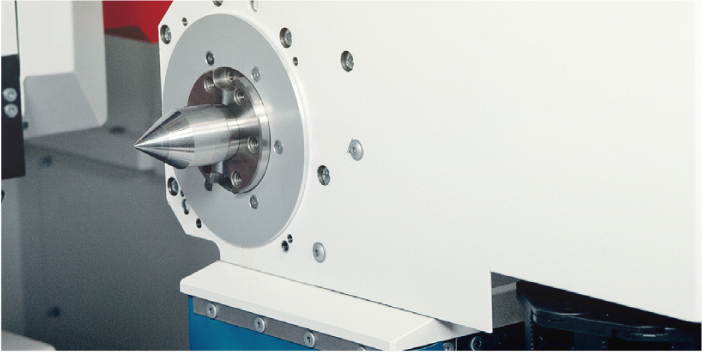
Talk to us about your efficiency in cylindrical grinding
Regardless of whether you want to optimize your current systems or equip new machines with all the refinements to be ready for the future: Contact us.Contact form We would be happy to assist you.