LaserControl - 精密加工のための最新レーザープロセス測定技術
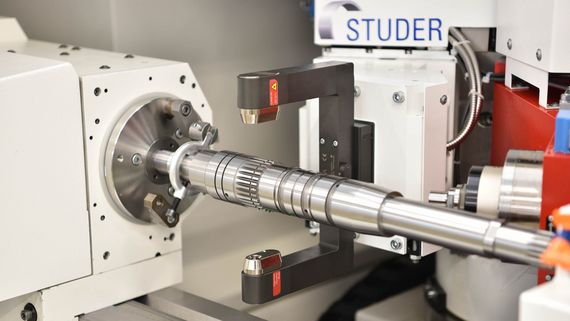
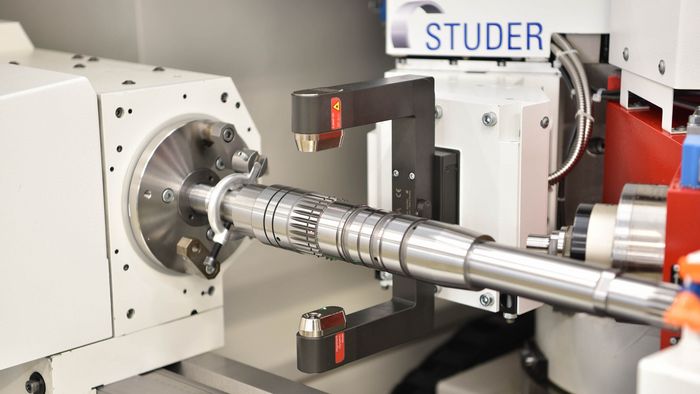
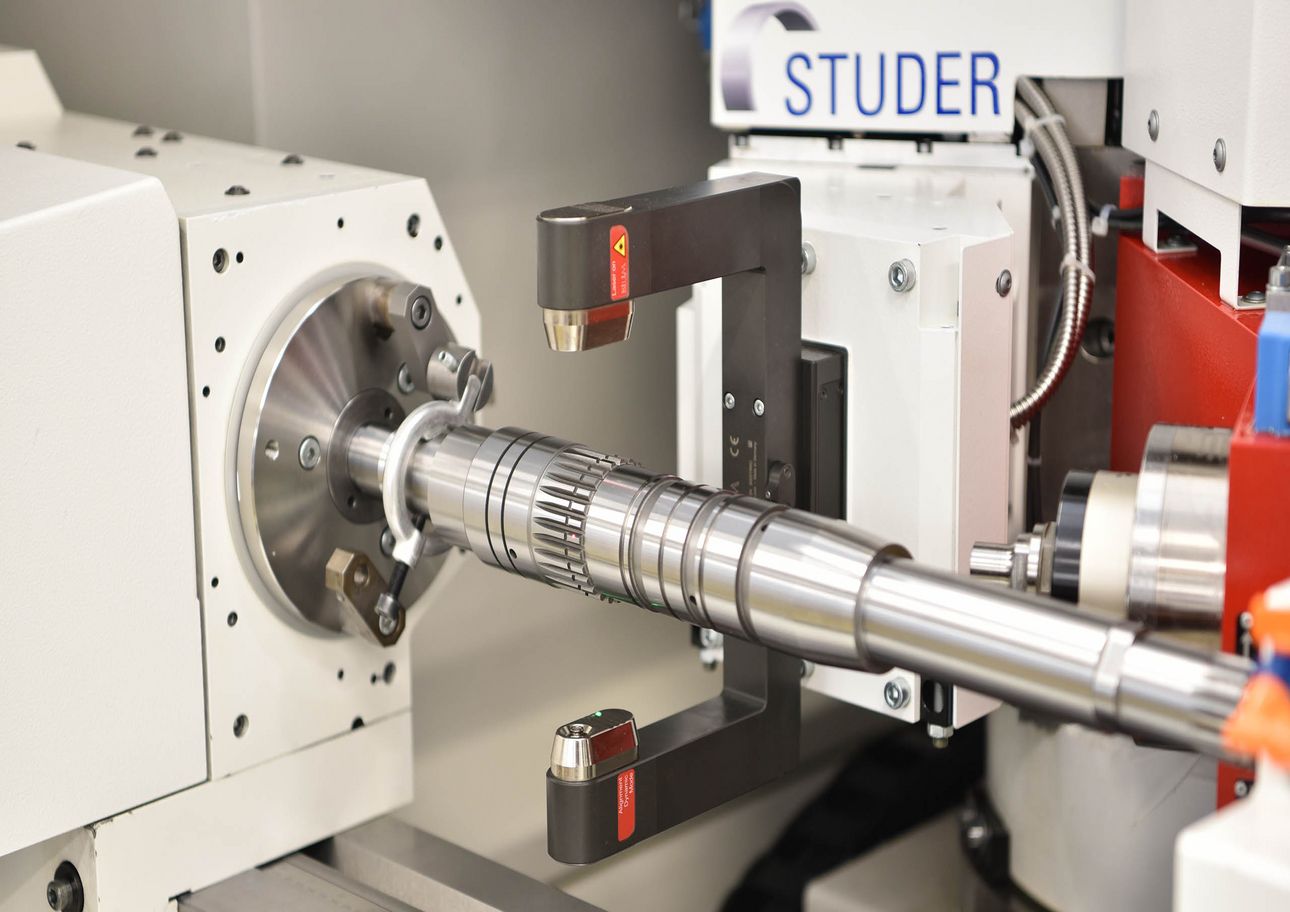
生産工程内での測定技術の需要
周知のように、研削機械の仕上げ加工では、寸法、形状、位置精度に関連した厳しい公差や、高精度な表面仕上げ面品質が求められることが多くなっています。これらの要件を満たすために、多くの場合、企業には培われた経験値があります。しかし、外部の測定機での中間測定とそれに対応する補正により、部品加工のリードタイムが長くなるため、特にバッチサイズが小さい場合には、機械上でのプロセス評価が求められています。これらの管理対策により、プロセスの信頼性と生産性を大幅に向上させることができます。理想的かつ望ましいのは、多種多様なワークピースに柔軟に対応できるソリューションです。
研削プロセスにおける様々なプロセス測定技術
STUDER複合円筒研削盤における機上レーザー測定技術
STUDERには、機上でのレーザー測定技術の使用において10年以上の経験があり、これは研削砥石やワークピースの測定のために使用されてきました。 将来の生産技術の動向に対応できるようにするため、STUDERではこのような基礎研究の長い伝統があります。この知識と経験が、今、顕在化しているニーズに対応するために活用されています。他の分野で工具監視に使用されているこのシステムは、研削盤上のワークピースを測定するため、ごく最近入手可能になった最新レーザー測定技術に基づいて、STUDER仕様に合わせさらに開発が進められました。 必要な測定装置(図4のUプロファイルを参照)は、対応する研削スピンドルを搭載した当社のB軸の測定プローブと同様に、機械的に取り付けられています。実際、このような状況はオペレータにとっては見慣れないものではありません。
この測定装置のサイズは、ワークピースの直径に合わせることができます。測定中にワークピース表面を吹き払うための既存のエアノズルと、新開発の汚れ防止シールドにより、機械内のクーラントからレーザー光学系を効率的に保護します。レーザーユニットのメーカーは、先代モデルに比べて、より開発が進んださらに高精度のレーザー光学系も採用しています。しかし、我々から見て最も印象的なのは、ワークピースが回転しているときに評価用の何千もの測定点を生成できることです。これにより測定時間が大幅に短縮されます。これらの機能を、STUDER固有の測定サイクルに統合することができています。これによりユーザーは、精密ワークピース加工のための適切な非接触式測定方法を利用できます。
様々なサイズの直径を1台のレーザー測定装置で測定できるだけでなく、キー溝や縦溝を有するシャフトや直径範囲の歯車のような「途切れた」直径についても、1台のレーザー測定装置で精密な確認測定が可能であることに、ここで言及しておかなければなりません(図2参照)。以前に使用されていた接触式定寸測定装置でのセットアップと再段取の作業がなくなっています。この措置により、効率が劇的に向上します。
測定サイクルは、各加工または研削プロセスの終了後に任意に選択できます。STUDERソフトウェアは、各測定サイクルの後に直径あたりの測定値を記録します(図3参照)。このプロセスにより、オペレータは、研削された部品の品質を一目で確認することができます。
切削工具へのレーザー測定技術の応用例
機上測定の非常に効率的な使用例としては、小ロットでのPCD工具の複雑加工があります。ここでよく問題になるのが、何が何を加工しているのか、ダイヤモンド砥石が工具を加工しているのか、あるいはその逆なのか、という点です。このために、接触式測定装置によるいわゆる「クローズドループプロセス」がよく用いられています(図3)。刃先を測定、研削、測定というように、工程が何度か繰り返し行われます。非常に優れた結果として、この措置により、直径公差±1.5マイクロメートルが実現されます。この用途では、PCDの刃先が接触式測定部に敏感に反応する場合があるため、非接触式測定を希望する声が多くなっていました。
この公差範囲における、刃先またはガイドレールを有する工具の非接触式測定を求める声には、上述した機上レーザー測定技術(図4)によってついに対応できるようになりました。この分野で必要とされる代表的な測定は、例えば以下のようなものです。 刃先のある工具の測定において、1つの測定面内で刃先の最小直径と最大直径を検出します。 切削工具の2つの異なる面での測定、つまり回転によって生成された円筒を異なる面で測定することにより、切削工具において希望するテーパの寸法が与えられ、これを出力することができます。
切削工具の同一面内での刃先とガイドレール部の直径の寸法差によっては、レーザー光学系は、ワークピースを回転させながらでも、これらの直径を検出することができます。これはほとんどの工具に当てはまり、測定時間の短縮に良い効果を発揮することになります。
工具シャフトの端面部、刃先の振れがどれだけ大きいのかを、研削する工具をクランプした状態で加工前に知りたい場合、STUDER測定サイクルが役立ちます。
結論
紹介した機上レーザー測定技術により、研削盤におけるプロセス測定技術したアプリケーションの可能性が広がります。精密な複合非接触式測定プロセスは、精密加工の高効率化に向けたユーザーの努力をサポートします。