How is digitalization changing machine manufacturing? And which innovations are there in grinding technology? Talks on these issues will invite discussions at the Grinding Symposium.
Exciting presentations on current hot topics are an integral part of the Grinding Symposium. Many renowned social, economic, digitalization and machine manufacturing experts have already spoken here. And you can expect to hear top-level speakers once again this year.
All lectures will be given in German or English and simultaneously translated into English, German, French and Italian.
Wednesday 8 May 2019, starting at 2: 00
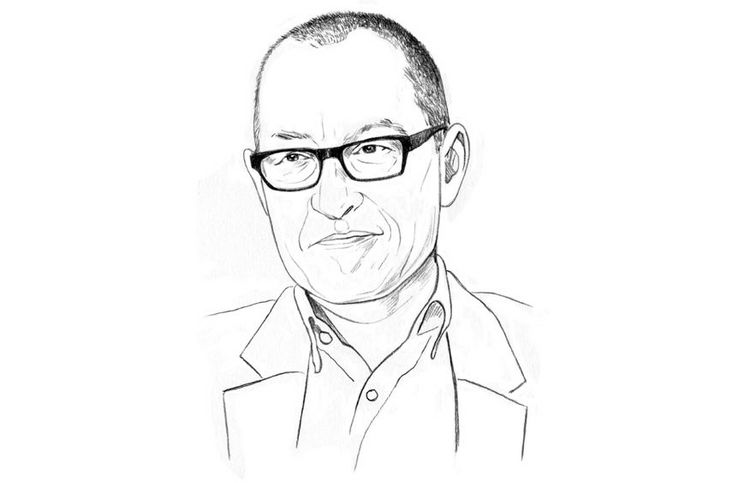
Human and machine –how can we best complement each other?
Thinking in ecosystems should replace thinking in industries. Digitalization and AI, Cloud and IoT create continuous patterns of change, which affect everyone. Human beings are still one step ahead in the competition with machines. This relates to cognitive and fine motor skills. There is even talk about the comeback of craft. Whether new or established companies take the lead in this process of change remains to be seen. However, the human element is crucial: Good or bad management makes the difference. We are all reliant on how human, artificial and emotional intelligence quotients interact.
Dr. David Bosshart is CEO of the Gottlieb Duttweiler Institute for Economic and Social Studies. Holding a PhD in philosophy, his areas of expertise are the future of consumption, social change, digitalization and especially the relationship between humans and machines
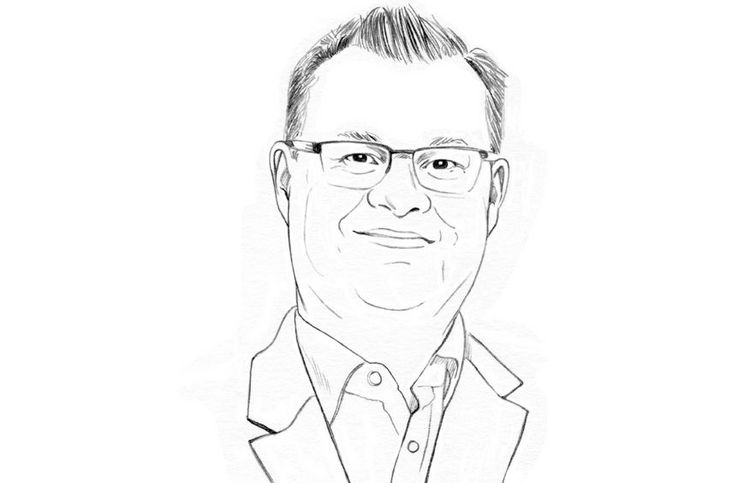
UNITED GRINDING Digital Solution™ – The customer benefit
Digitalization in the machine tool sector is more a generational issue than a technological. Key distinguishing features of modern machine tools will increasingly be found in the area of intuitive operation and handling in future. The supreme discipline of digitalization is to automatically perform optimizations on the basis of acquired data and to identify connections and patterns using smart data analysis. The success of our customers is the driving force of the UNITED GRINDING Group – and will remain so in the digital Age.
Christoph Plüss is Chief Technology Officer of the UNITED GRINDING Group. He has worked for the Group since 2009 and was previously Head of R&D and CTO of EWAG.
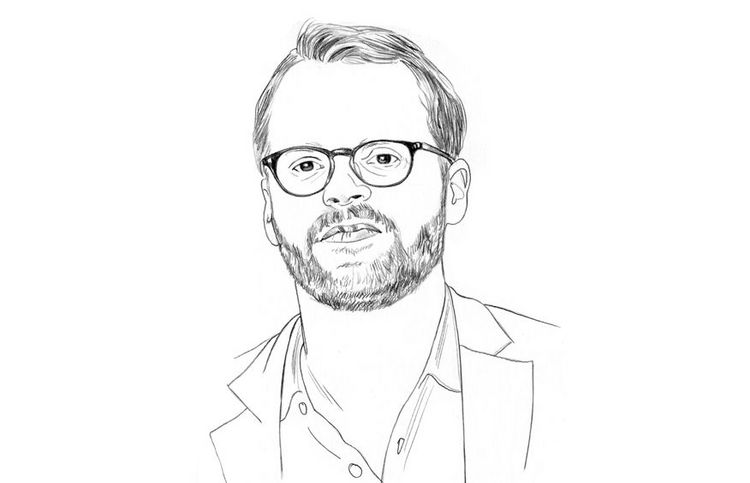
Artificial Intelligence – Towards machines that can continually adapt
Based on insights from artificial intelligence, robotics, and biology, new generations of machines can be created whose bodies and artificial brains are not limited to perform one specific tasks, but can instead evolve to handle a variety of tasks in changing real-world settings. Lifelong learning agents, for example for autonomous driving, will continually improve its performance and update its knowledge unsupervised, rapidly adapt to unforeseen context, and learn and consolidate new tasks without forgetting old ones. Artificial intelligence has the potential to significantly disrupt many different industries by replacing the traditional design and deploy approach with an iterative evolutionary approach of design, deploy and adapt.
Dr. Sebastian Risi is Associate Professor at the IT University of Copenhagen, Denmark
Thursday 9 May 2019, from 09.30
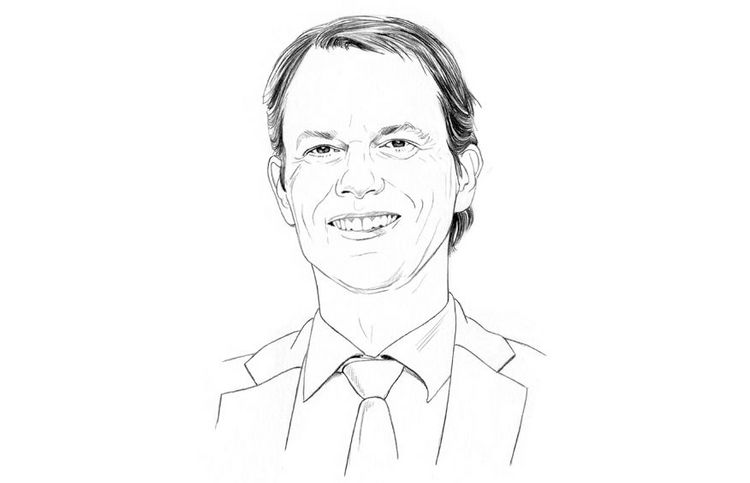
Assistance system-based process monitoring in grinding technology
Current developments such as customizing or new drive concepts in the automotive sector require agile process control using assistance systems in production. The prerequisite for this is sound, physically-based process knowledge. Digital twins are necessary to obtain this knowledge. Digital twins are data-based images of real components, tools and machines, which exist throughout the lifetime of the real object. They generate large data volumes, which can be analyzed for previously unknown trends and patterns using artificial intelligence methods, and help facilitate quality control.
Prof. Dr.-Ing. Thomas Bergs holds the Chair of Manufacturing Technology at the Laboratory for Machine Tools WZL of RWTH Aachen University
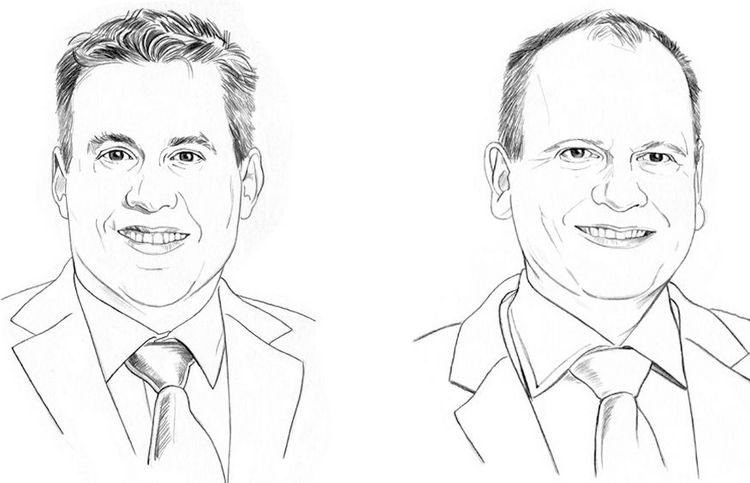
WireDress® in practice (practical examples and experiences)
Difficult-to-machine hard materials and rising quality standards place enormous demands on a reliable production process. Using a bond with a high dimensional stability, almost any profile can be precision-contoured in the μm range. Other important factors that contribute to reproducibility in the absolute range of less than 1 μm are a fully air-conditioned hall, automatic loading and unloading, adapted tooling, cutting-edge measuring technology, an efficient cooling concept and, of course, highly trained and motivated personnel.
Roman Rudolf is Head of Sales and Support, Thomas Schenk is Head of Production of FISCHER AG. The company based in Herzogenbuchsee, Switzerland, produces rotation systems such as precision spindles, electro-compressors and milling heads
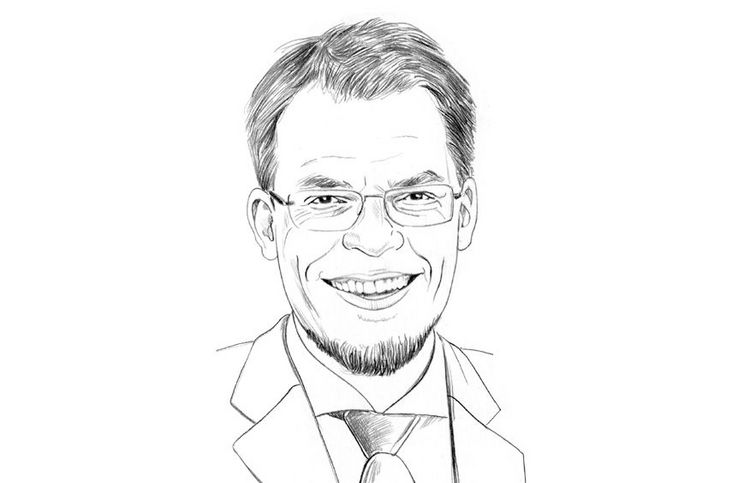
High-performance grinding… rapid development of various technologies
The efficiency of grinding processes depends on parameters such as cutting speed and grinding of the grinding wheel. A higher cutting speed results in improved grinding performance, but also increased heat generation, when the grinding wheel specification is appropriate. The grinding direction (same direction and reverse direction) is also an important factor in the chipping process. Analysis of the chip formation process taking account of grain characteristics leads directly to a suitable process design.
Dr. Stefan Bohr is Director of Application Engineering & OEM Management at Saint-Gobain Abrasives, a global manufacturer of abrasives
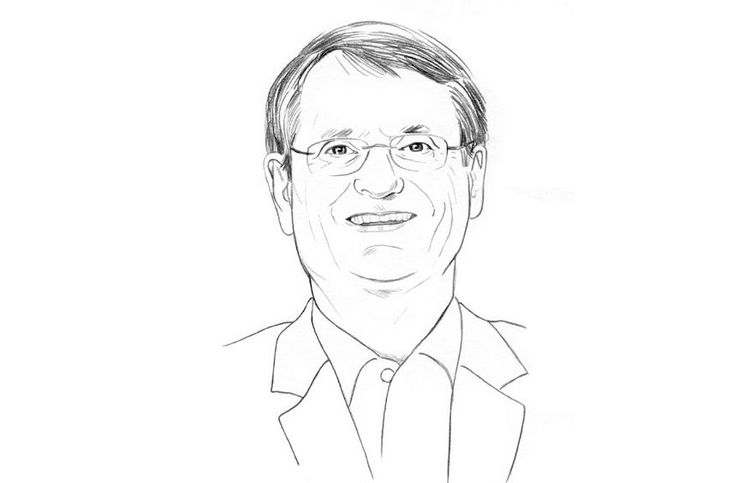
Potential and applications for machine learning in the manufacturing industry
Through condition monitoring of critical components and adapted maintenance measures, unforeseen machine failures can be avoided and system availability can be increased. Artificial intelligence provides the algorithms and methods necessary to process data efficiently and interpret it profitably. Digital twins make all data from the product development process available and enable it to be experienced by means of virtual reality technologies. In order to ensure efficient production, production systems must monitor the state of wear of functionally relevant components and adapt their behavior according to the situation.
Dipl.-Ing. Eckhard Hohwieler is Head of Department at the Fraunhofer Institute for Production Systems and Design Technology (IPK) in Berlin
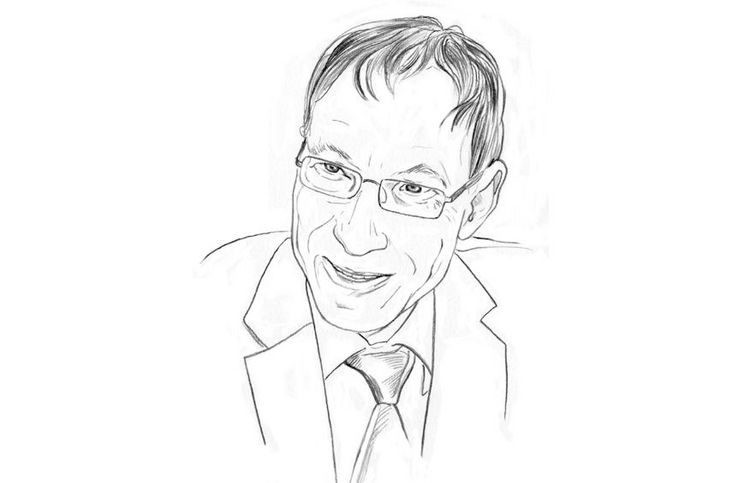
Vision and developments in grinding machine technology
Without grinding technology, future technologies such as optics and electronics as well as classic machine manufacturing are inconceivable. Major lines of development in production technology today are Industry 4.0, artificial intelligence and biological transformation. This generally involves a further intensification of automation. An important application of artificial intelligence will in future also be the service sector in the sense of predictive or assessment-based maintenance, and accuracy improvement via self-learning compensation algorithms. The future will see a more intensive collaboration between machine manufacturer and machine user, with the need to protect reciprocal security and confidentiality interests.
Prof. Dr. Konrad Wegener is Head of the Institute for Machine Tools and Production (IWF) at ETH Zurich
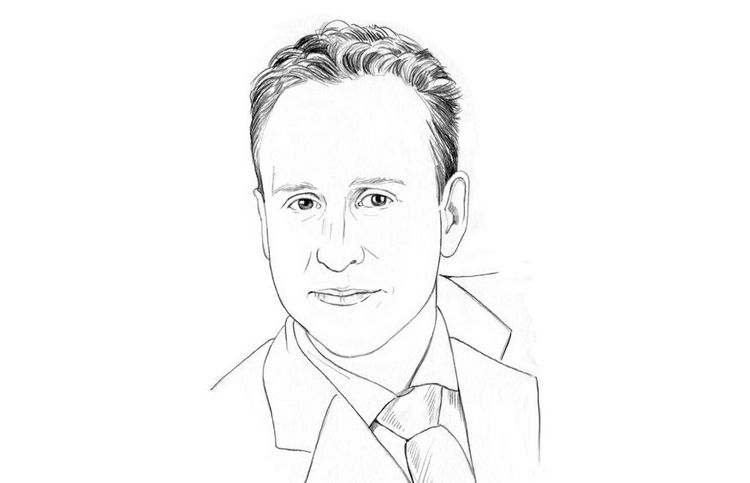
Process-adapted grinding tools and innovative wheel bodies
Only through the optimal interaction of machine tool, coolant, conditioning process, process settings and grinding tool can high removal rates, high productivity and high-quality workpieces be achieved. The geometrical and mechanical characteristics of the abrasive grain materials decisively define the chip formation mechanisms, the grinding force generated and the wear behavior. Shape, material as well as mechanical and dynamic characteristics of the grinding wheel body influence the vibration and damping behavior of the grinding wheel.
Dr.-Ing. Markus Weiß is Head of Grinding Technology at TYROLIT Schleifmittelwerke Swarovski KG
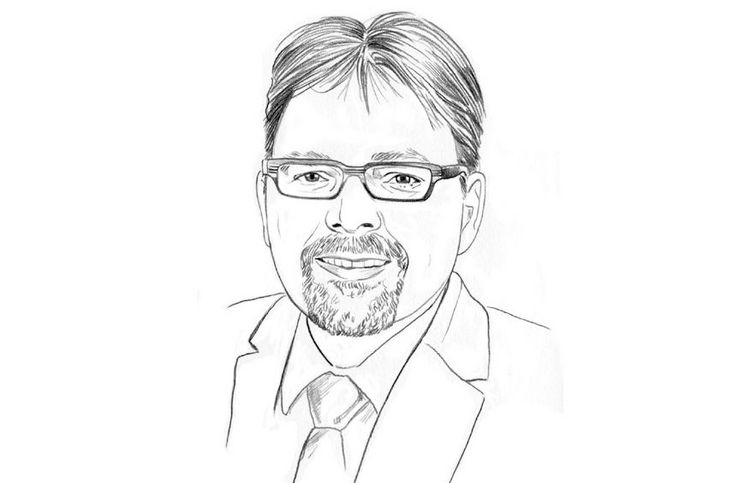
Coolant supply conditions as the key to process capability, energy efficiency and peripheral zone influencing during grinding
Significantly improved machining conditions can be achieved through effective coolant supply to the grinding slot. The thermomechanical loading of the workpiece can be reduced and the process performance increased, without negatively affecting the peripheral zone of the workpiece. Thanks to flow-optimized coolant nozzles and smaller coolant quantities energy consumption decreases, and coolant systems can have smaller dimensions. The cost-effectiveness of the grinding process can be significantly increased as a result. Practical examples show a potential of 20 to 30 percent.
Prof. Dr.-Ing. habil. Carsten Heinzel is Deputy Head of the Main Production Technology Department at Leibniz Institute for Materials Engineering (IWT) and Honorary Professor at Bremen University
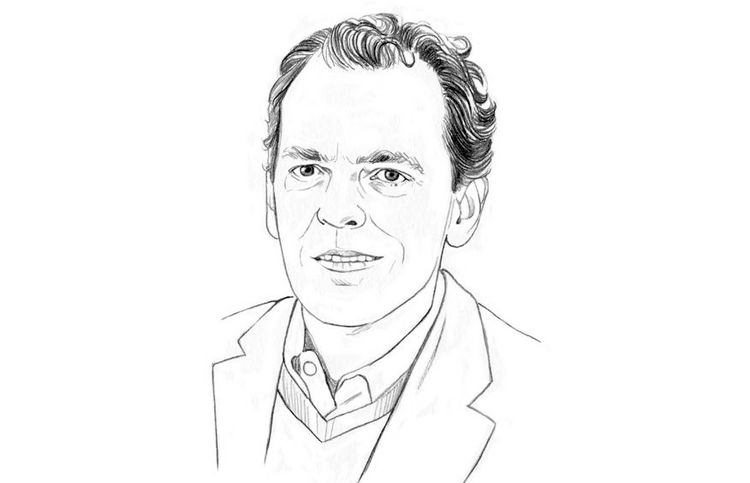
Effectively and demonstrably improve the profitability of your company with the liquid tool!
Influence of coolant on manufacturing costs is often ignored in reality. The savings in the form of higher productivity and increased machining quality correspond to a multiple of the capital used for coolants and grinding oils. To verify this, all relevant key points of machines, process, workpiece and materials are recorded in a situation analysis. The savings are higher if a high-performance, stable and well maintained machine is used.
Marc Blaser is CEO of Blaser Swisslube AG, an international coolant manufacturer, which has been in family ownership for three generations
Friday 10 May 2019, from 9.30
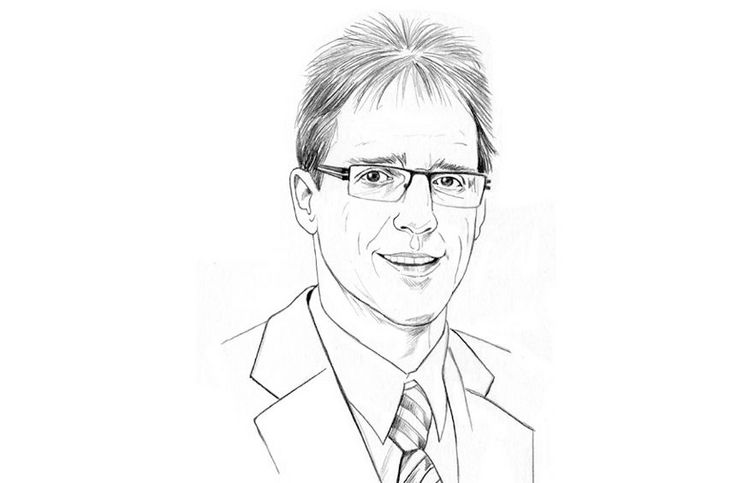
Avoidance of grinding burn and clogging through targeted coolant supply
A targeted coolant supply is necessary for efficient process control during grinding. Coolants fulfill different functions, for instance cooling and lubrication of the grinding slot and the contact zone. The right amount of coolant is crucial: too much will make the action point float, and too little will cause thermal damage to the peripheral zone.
Prof. Dr.-Ing. Wilfried Saxler is Head of the Institute for Machine Tools and Manufacturing Technologies at the University of Applied Sciences in Cologne
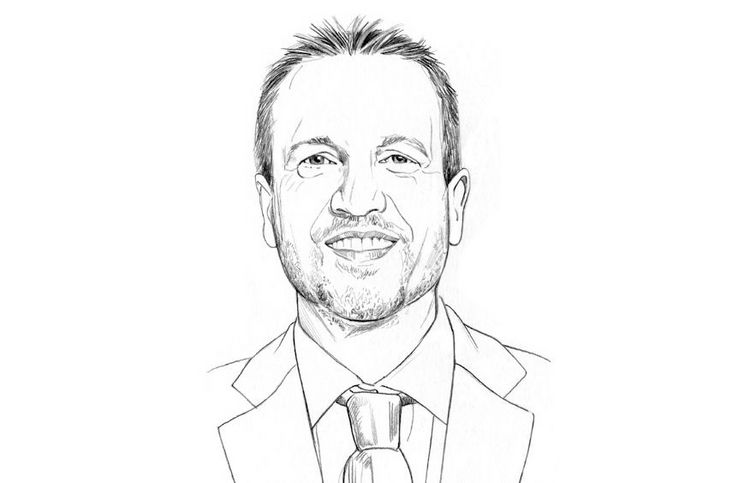
Trends in tool development and their implementation
The requirements of climate protection have an impact on the development of machining tools. Constructive changes and new machining strategies are required. For the machining of lightweight components made from aluminium lithium alloys special milling cutters with very high cutting speeds are required. Material groups such as ISO M, which are difficult to machine, can be machined efficiently and reliably with Dynamic Cutting. Machine data analysis in real time helps reduce the machining time per workpiece and increases process reliability and machine service life.
Wolfgang Vötsch is Senior Milling Product Manager at Walter AG
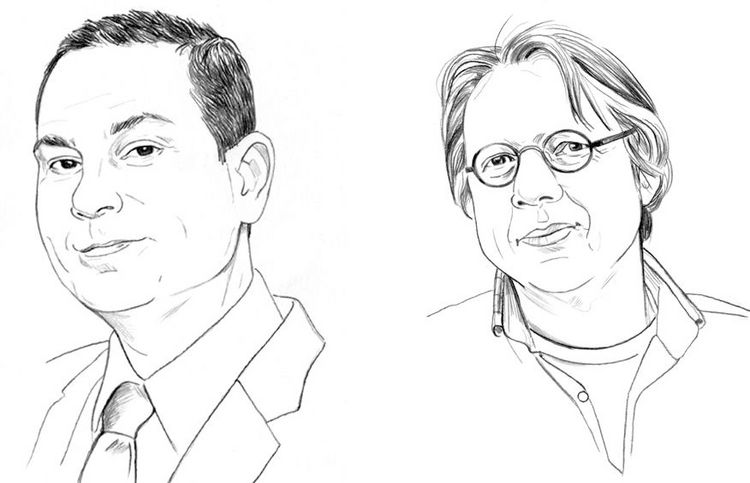
Think Laser! on tools and 3D geometries
The production of spiral tools in solid material on a laser machine tool enables autonomous production of individual tool geometries. A customer application was developed for the van Frankenhuyzen B.V. company in a joint study. The machine has a storage area with blanks of different diameters in the automation cell. The customer can configure and order any tool via the webshop. This enables automated production in small series, including a lot size of one.
Dr. Claus Dold is Head of Process Innovation at Ewag AG and responsible for the development of new machining processes and applications
Jan van Frankenhuyzen owns the van Frankenhuyzen B.V. company in Lexmond, Netherlands, which manufactures high-quality tools in small series
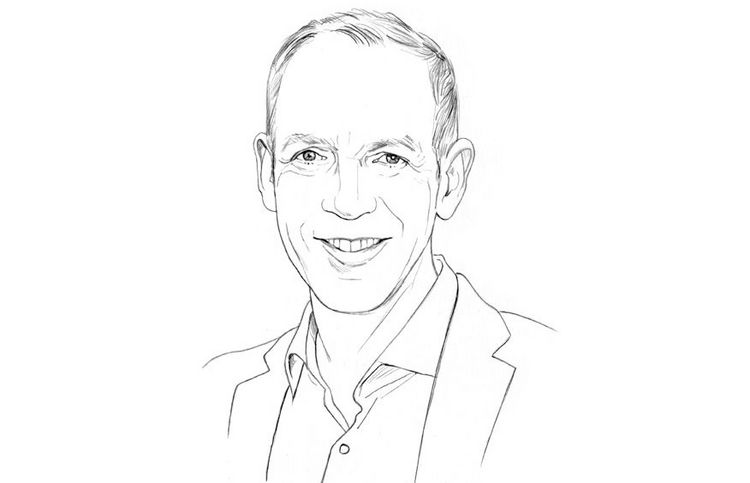
Key to successful change: Fulfilling the highest tool requirements in terms of quality and service with high-tech and passion
High-tech and passion alone are not enough to cope with quickly changing tool requirements. It is the interaction of the factors of technology and processes on the one hand and people on the other, i.e. management, employees, customers and business partners. The better these factors are interlinked, the better the interaction between hightech and passion will work, and the more successfully change can be managed.
Achim Kopp s Managing Director of Kopp Schleiftechnik, a manufacturer of cutting tools for milling and drilling of metals and plastics