
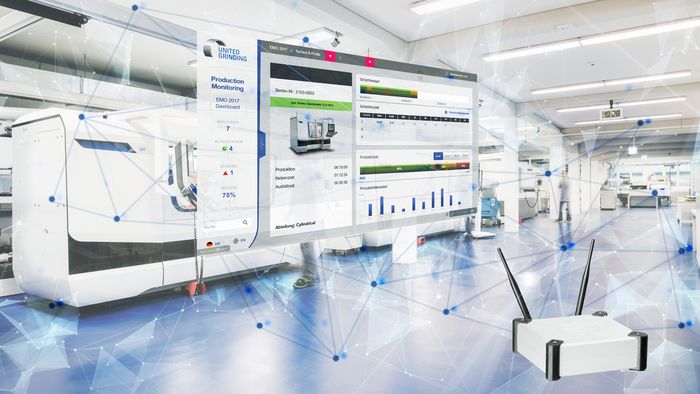
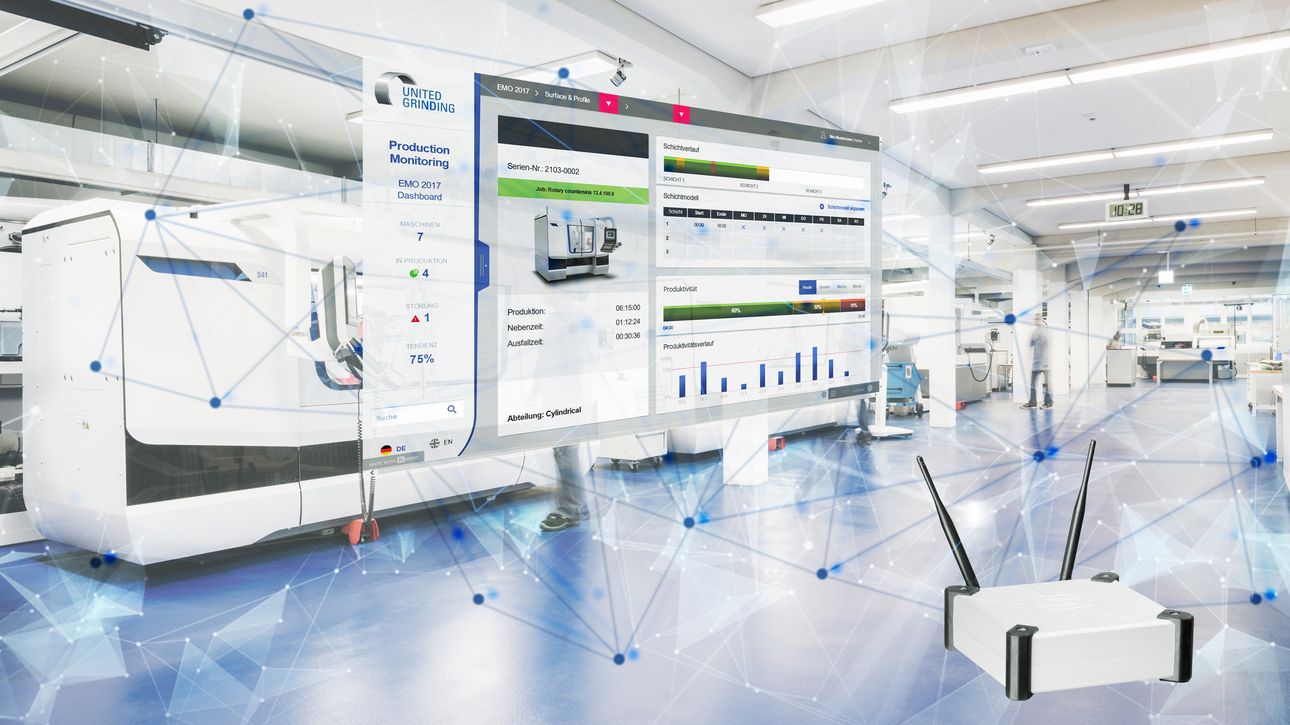
Digital Solutions
All machine exhibits of the symposium will be live and online in the digital control station of UNITED GRINDING Digital Solutions™. Current machine conditions can be checked on the PRODUCTION MONITOR, upcoming maintenance work can be monitored on the SERVICE MONITOR. SERVICE REQUESTS are sent at the push of a button to establish a direct and secure data link to the customer care team. If service support is required, direct digital assistance can be provided by the REMOTE SERVICE and the new CONFERENCE CENTER. For the first time, visitors can also experience the connection of third-party machines to UNITED GRINDING Digital Solutions ™products in FutureLAB. In the area of Condition Monitoring and Predictive Maintenance, we will be presenting the first concepts for generating digital fingerprints of the main axes. These will make it possible to quickly compare machine conditions.
New technologies
Technological advancements in high performance materials continue to pose new challenges for grinding and machining processes. Therefore, new, complementary technologies such as EDM (Electrical Discharge Machining) or non-contact measurement technology have counted among the Group's core competencies for some time. State-of-the-art laser technology is used for machining super-hard materials. Current research is focused on new femtosecond lasers for cold micro-material processing. The Group is already able to produce focus spot diameters of less than one micrometer using special laser processing lenses. In future, this will also enable microcomponents to be manufactured in all possible materials.
INNOVATIVE OPERATING CONCEPTS
The vision of UNITED GRINDING Group is to control machines by gestures, language or glances. "We consider this to be a groundbreaking way to simplify the operation of our high-end machines in the future and unify their control across the entire Group", says Plüss. The HMI (Human Machine Interface) is designed to adapt to the operator's capabilities, needs and core tasks. For example, a shift worker will only be provided with the functions they need for part production; an experienced service technician will have access to relevant processes and diagnostic functions.
ADDITIVE PRODUCTION
Industrial 3D printing is a future topic that also interests UNITED GRINDING Group. In collaboration with IRPD AG, the Group provides 3D printing services in plastic and metal for internal and external customers. "In the future, SLM (Selective Laser Melting) technology could become relevant as a significant prototyping method for producing complex, metallic components", says Plüss. In combination with their expertise in precision machining and digital networking of manufacturing processes and machines, the Group is developing the value chain from metal powder to the ready-to-use component. They call this "Powder to Part® / P2P®".